How Chevrolet Started, Grew & Became $11.5 Billion Company

Success Secrets TV:
How Chevrolet Started, Grew & Became $11.5
Billion Company
The name Chevrolet originated from a Swiss-born
American racer Louis-Joseph Chevrolet, who
founded his company with William Durant in
1911, stayed for four years and then left
his own company to Durant in 1915.
The Chevrolet Company previously called the
Chevrolet Division of General Motors Company
and simply called the Chevy is the automobile
department of General Motors, a manufacturing
company in the United States.
How Chevrolet Began
Twenty years before Chevrolet, Durant was
the founder of a successful Durant-Dort Carriage
Company which manufactured horse-drawn vehicles.
And so Durant wouldn't even touch a car with
a ten-foot pole, let alone allow his daughter
to ride in what he called, "loud and dangerous
horseless carriages."
But as time passed he realized that there
were more cars than carriages on the American
streets; an experience that did not settle
well with the relatively tentative public.
As the government regulated cars for their
safety, Durant had other ideas.
Why not improve the security of these cars
instead?
In 1904, Durant approached a struggling Buick
Motor Company and became its controlling investor.
Within a span of four years, Durant demonstrated
his salesman attitude and transformed Buick
into a leading automobile name amongst the
likes of Ford, Oldsmobile, and Cadillac.
For Durant, however, it was only the start.
Durant figured he could further improve his
odds in the industry if he built a holding
company that would control several automobile
divisions, with each division manufacturing
their own car.
With the Buick's outstanding profits, Durant
had sufficient capital to found the General
Motors Company in 1908.
A year later, General Motors acquired several
car brands like Buick, Oldsmobile, Cadillac,
Elmore, and others.
Unfortunately,Durant got so carried away in
his "automobile acquisition crusade" that
GM suffered cash shortage with their sales
losing to Ford's.
And so, in 1910, General Motors showed Durant
the exit door.
But Durant did not give up.
Having regained his bearings, he reunited
with an old colleague from the days of the
Buick motor company, Louis-Joseph Chevrolet.
Durant knew the Swiss-born American as a man
whose competency for car mechanics matched
his passion for racing.
In 1909, Louis had participated in the Giant
Despair Hillclimb.
An oddly apt name, considering the Hillclimb
race was less about the racers themselves
and more about test-driving the competing
car brands they drove.
Therefore, when Durant offered a chance to
build more automobiles, Louis couldn't resist
signing his name on the dotted line alongside
Durant's.
In 1911, Louis co-founded the Chevrolet Motor
Company with Durant.
Durant used Louis’ racing status as a means
of building a motor company, and his way of
getting back at General Motors.
The first Chevrolet car, the Series C Classic
Six was designed by Etienne Planche with directions
by Louis.
The prototype was ready before the company
was incorporated even though the production
didn’t happen until 1913 where it was introduced
at an auto show in New York.
In 1914, Chevrolet redesigned its logo.
And so a "bowtie emblem" logo was used on
Chevrolet’s first produced cars in 1914:
the Chevrolet H series and L series models.
That same year, Durant and Louis argued about
their differing intentions for Chevrolet’s
future car designs.
Durant wanted simple and affordable cars that
would surpass those of Fords.
On the other hand, Louis preferred playing
it fast and loose, with luxury or racing cars.
These differences split these two associates
and Louis sold his shares of the company to
Durant.
Now alone at the helm, Durant was able to
focus on his next winning car design.
He achieved this in 1916 when the cheaper
Chevrolet Series 490 finally outpaced Ford
in sales and cemented Chevrolet’s place
among the big automobile names.
To say Chevrolet made huge profits during
this period would be a severe understatement.
Durant revisited General Motors as a controlling
investor, purchasing their stocks, which gave
him the leverage to launching himself into
leading General Motors once more.
By 1917, Durant had become the president of
General Motors.
All was right, now that Durant's "big automobile"
dream was back on track.
And of course, his first directive was merging
the highly successful Chevrolet into the parent
company General Motors as a separate division.
How Chevrolet Grew
In 1918, Chevrolet launched a new V8 powered
model, the Series D for open two-seat cars
and the touring cars that could seat 5 passengers.
These models didn't sell well though and they
were scrapped by the next year.
Given Chevrolet's successful track record
in the market, General Motors rebranded and
sold their commercial grade cars and trucks
as Chevrolet with similar appearances with
the Chevrolet’s vehicles in 1919 from Chevrolet
factories located in Flint, Michigan.
The automobile company built several branch
assembly plants in New York, Ohio, Missouri,
California, Texas, and Canada.
Somewhere between the 1920s and 1940s, Chevrolet
would see Durant's vision for "producing simple
and affordable cars" come true.
In fact, Chevrolet, Ford and Plymouth were
known to Americans as "the low priced three".
During this period, one of Chevrolet's most
notable cars was the Stovebolt introduced
in 1929, which was tag-lined "a six for the
price of four".
This and several generations of the car model
blew away the competition of Ford and Plymouth.
In 1953, the Chevy Corvette, a sport’s car
with two seats and a fiberglass body debuted
to become the first mass-produced sports car
in the United States, championing the "America's
Sports Car" appeal.
The appeal of the Corvette and other Chevrolet
passenger cars would be enhanced with the
first-time introduction of Rochester Ramjet
fuel-injection engine as a high-performance
option for the price of $484.
The Chevrolet small block V8 car design made
its debut in 1955 and remained in circulation
longer than other mass produced engines around
the world.
Modifications to the V8 engine including the
aluminum block and heads, the electronic engine
management and the port fuel injection gave
birth to the designs in production today.
In 1958, Chevrolet introduced the Impala series,
which went on to become one of the best-selling
American cars in history experiencing popularity
during the 60s and 70s.
The parent company General Motors introduced
Chevrolet to Europe in 2005.
With rebranded cars manufactured from the
General Motors branch in Korea acquired Daewoo
Motors.
The economic depression between 2007 and 2010
hit Chevrolet hard.
But the road to recovery began in 2010 with
the introduction of fuel-efficient cars and
trucks to compete with foreign automobile
manufacturers.
Within the same year, Chevrolet introduced
the plug-in hybrid electric vehicles, Chevrolet
Volt in America, which was sold under the
name Opel/Vauxhall Ampera throughout Europe
with a record 5,268 units soldand became the
world's best-selling plug-in hybrid electric
vehicle (PHEV) car in 2012, winning the award
for the North American Car of the Year, European
Car of the Year and World Green of the Year.
The series was then named the combined Volt/Ampera
that was sold across the world.
It exceeded the 100,000 unit sales milestone
in late 2005 and eleven years later the Volt
family of vehicles had become the world's
best-selling plug-in hybrid as well as the
third best selling electric car after the
Tesla Model S and the Nissan Leaf cars.
In 2011, Chevrolet set a global sales record
of 4.76 million vehicles sold worldwide
In late 2013, the Chevy brand was withdrawn
from Europe by General Motors leaving the
Corvette and Camero lines.
In 2016, Chevrolet unveiled the first affordable
mass-produced all-electric car the Chevrolet
Bolt EV.
This car too has won several awards.
Where Chevrolet Is Today
Chevrolet now has its headquarters in Detroit,
Michigan, and operates throughout 140 countries
in North and South America, Asia, Australia,
South Africa, and Europe with over two million
vehicles sold annually in the US alone and
a brand value of $11.5 billion.
Thank you very much for watching our videos.
We’ll like to give you another interesting
video for you to enjoy next but before then,
our team will be very happy if you can like
this Video and share it with your friends
on social media.
If you’re new here, don’t forget to subscribe
so you won’t miss other interesting videos
like this.
Look at your screen now to see two other videos
we handpicked for you to enjoy next.
We love you
Why GM Failed In India
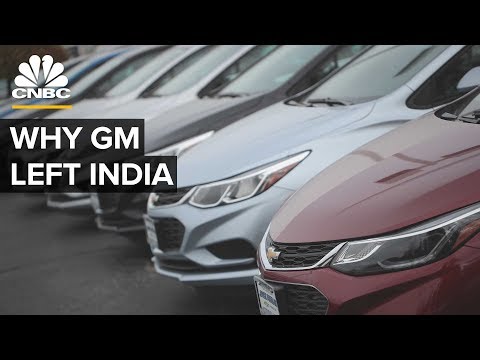
CNBC:
Over the last 20 years, the
Indian automotive market has grown from
about 500,000 new passenger cars,
hatchbacks, sedans and utilities to
about 3.5
million in 2018.
The market has an expected compound annual
growth rate of about 5 to
6 percent over the next 10 years.
But, some automakers have struggled
to make it work.
Among them is General
Motors, the largest U.S.
car company. GM stopped selling cars in
India in 2017 after years of
declining market share.
It's a striking move for GM, which
in recent years has also closed
shop in other regions around the
world, as leadership focuses on
maximizing profits and making investments
in new technologies such as
electric power trains
and mobility services.
With a population of more than
1 billion people, India is becoming
one of the world's
largest automotive markets.
The country is poised to surpass
Japan as the world's third biggest
new car market in 2021.
So while there is ample
opportunity for automakers, the Indian
landscape has been particularly difficult
to navigate, especially for
American firms. GM watched its share
of the Indian market erode
steadily over several years, bottoming out
at about one percent in
2016 just before the
automaker pulled out.
So if the Indian market is
growing, why did GM struggle, especially
when GM has been
so successful in China?
To be fair, quite a few automakers
tend to have difficulty in the
Indian market. First of all, India
is a massive country with a
diverse population of roughly 1.3
billion people.
India, I think, we are
definitely a complex market.
The income levels
are quite heterogeneous.
We are divided, actually into
urban India and rural India.
The consumer requirements are actually
different even the needs are
different in both these markets.
There are a few criteria a
mass market automaker ought to meet.
They are fuel efficiency, resale
value, proximity of service stations
and the affordability of parts
and low servicing costs.
I think first thing is price.
We are a country with a
very low per capita income.
Indians are very price sensitive.
But price is not the only factor.
So now the customer also needs
some more value, for example, with
styling elements. And then, I think,
the consumer also wants a global
brand. They want a
brand which is aspirational.
The consumer wants an overall combination of
all P's, you know it may
be product, it may be
price, it may be positioning.
Which makes the things
quite complicated for OEMs.
These might seem pretty attainable,
but many automakers have
struggled to meet these
in the country.
There are a couple of companies who
have managed to crack that code
and there are several more with shares
of the market ranging in size
from small to smaller.
By far, the most successful automaker
in India is the Japanese firm
Suzuki, which alone owns
half the Indian market.
Suzuki has enjoyed something of
a first mover advantage.
It was the first major automaker to
enter India, and it did so
through a joint venture
with Indian manufacturer Maruti.
Suzuki also specializes in highly
fuel efficient vehicles, which are
extremely important in
the Indian market.
After Suzuki, Korean maker Hyundai is
the second largest with 16
percent of the Indian market.
After that, Indian, Japanese and Korean
makers such as Honda, Tata,
Kia and Mahindra all more or less
have equal degrees of market share.
Kia in particular, is a relatively
late coming brand that has been
able to succeed in India.
I think an excellent example is
Kia Motors which recently entered, it
was a new brand and
they gave a great proposition.
They were in an SUV segment and
I think suddenly right from the month
one, we saw a great success
for this OEM, in India.
Then the remaining 10 percent of the
market is made up of others such
as Ford, Renault, BMW and Nissan.
Early on, GM entered the India market
with its Opel brand, a mass
market brand GM had
owned in Europe.
While Opel cars tended to be
affordable, they failed to resonate with
Indian buyers.
I think later on they realized that's
not a brand which is really
going to work well in India because
that was not a value proposition
which they were offering
to their customers.
But then GM introduced its Chevrolet
brand to the country, which
brought it more success.
It was a great success.
They launched a few great
products like Chevrolet Cruze Chevrolet
Beat. They had that start which
they were really looking forward.
Despite these efforts, the automaker had
trouble taking share in the
Indian market. It was the first
automaker to introduce a diesel fuel
powered car of its size.
At the time, the Chevrolet beat
was the smallest diesel powered car
customers could buy in India.
It was a strong proposition and
benefited from a government subsidy
on diesel engines.
But in the end, the
diesel Beat had few takers.
The company may also have made a
misstep by trying to introduce a
low-cost vehicle GM manufactured with
its Chinese partner SAIC called
the Chevrolet Sail.
Their plan got derailed with the
introduction of Sail because I think
they underestimated the consumer aspiration
and then, I think, the
decline started. GM also fell victim
to a kind of self-reinforcing
cycle. One challenge it struggled with
was the lack of an adequate
dealer and servicing network.
More premium brands such as Mercedes
and BMW often attract customers
with the means to travel
further for service and sales.
But, mass market brands such as
GM's Chevrolet are targeting middle
class buyers who value convenience.
Dealerships in India often sell a
single brand so GM's low sales
volumes meant a single dealer might sell
only a handful of cars in a
month and risk taking losses on
the costs of running the business.
In the end, such low market share
made it difficult for GM to justify
maintaining a presence
in the country.
The automaker officially stopped selling
cars in India on December
31, 2017.
GM told CNBC it explored many
options for its India business, but
ultimately withdrew after it
determined the increased investment
originally planned for the country would
not deliver the returns of
other global opportunities.
It continues to operate services
for existing Chevrolet customers in
the country. In September, the
automaker entered a long-term
partnership with Tata Consultancy Services,
which will do engineering
design for GM vehicles meant
for markets around the world.
The move out of India was part
of a larger pullback GM has been
making around the world as
it restructures its business.
We're seeing other automakers follow
suit as they're pruning.
They're pruning the dead branches and
focusing on where they can be
strong. For GM, this is a huge shift
because GM of old used to be all
things to everyone everywhere.
And, it has now decided that
is not the proper strategy.
The automaker told CNBC if it doesn't
see a clear path to leadership
and long term sustained profits in
a particular market, it will look
at opportunities to focus its resources
on areas that will lead to
the greatest results. It added that this
is the same approach it has
taken elsewhere.
The automaker also sold its
European operations to French carmaker
PSA in 2017.
At the time it pulled out of India
GM had two factories there, one in
the Gujarati city of Halol
and another in Talegaon.
The Halol plant was acquired by
MG Motor, the once famed British
brand now owned by Chinese
automaker SAIC Motor Corporation.
GM has a joint venture with
SAIC to produce cars in China.
Reports surfaced in November 2019 that
SAIC is also in talks to
acquire GM's Talegaon plant, along
with fellow Chinese automaker
Great Wall. GM told CNBC it
is exploring strategic options for the
plant. The move out of India was
a retreat for GM and for American
auto industry. Ford is starting
to do the same.
It's trimming some
of its offerings.
Global economy and global auto
market is slowing some.
Certainly true here in the
US, it's true in China.
There's just not enough money to
go around to every single market,
too every single vehicle line.
Look at Daimler and BMW,
they've announced major employee cuts.
But in some ways it might
have been a shrewd move.
The other thing that is happening
in the market that has never
happened before is we are on the
verge of massive disruption of the
industry. You know, we're going to
have a future of electric
vehicles, autonomous vehicles and new
ways to acquire personal
transportation and now
mobility service.
There's all kinds of things.
Nobody knows when that's going to happen
or how it's going to happen,
but it's requiring a
lot of investment.
Companies like GM just can't keep putting
a ton of money into the
future as well as a ton
of money in today's stuff.
While analysts do expect the
Indian automotive market to continue
growing in the foreseeable future, it
did hit a slump in 2019.
Maruti Suzuki sales were growing
until February 2019, but have
slipped every month, year
over year, until October.
Suzuki said in November that the slowing
Indian market was one of the
factors behind the company's falling overall
sales and net income in
its second fiscal quarter.
So I think right now the
market is going through turmoil.
Our economy is struggling and if
we only talk about the automotive
market we are talking about a decline
of minus 14 percent in 2019
calendar year light vehicles.
So obviously this year is the
kind of degrowth happening, which has
not happened in last
two decades, in India.
2020, we are just talking about a
kind of a flat growth but then
going forward, in 2021, '22, '23,
the assumption that our economy
should be back, you know, the
GDP growth rate will start growing
above seven percent. Indian
automotive analysts note the country's
auto industry has to contend
with the relatively recent rise of
mobility services such as ride
hailing. The potential of these
competing technologies is still
unknown, but could affect how
interested in car ownership Indians
remain in the future.
In the end, GM did make some of
the right choices when trying to go
into India. GM was right in
terms of localizing their products
typically for the Indian market, making
it, in line with the taxation
because they were able to save tax.
But, at the end of their day, were
really not able to match with what
the competitors were offering.
If the Indian economy picks back up,
GM may find itself trying to
profitably re-enter the country.
GM's rival Ford, which has been in
India since 1995, said in October
2019 it will create a new
joint venture with Indian manufacturer
Mahindra, which Ford said will help
it develop new products faster
and drive profitable growth.
How Saabs were made in 1960 - Saab factory in Sweden - engine and car production - Eng. sub
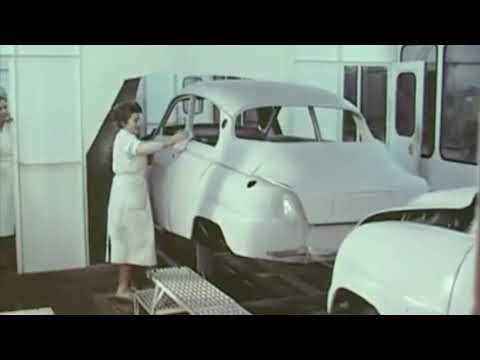
Adora Basil Winterpock:
Gothenburg is the site of Saabs production of engines and gearboxes.
The factory currently has a capacity of 30,000 engines and transmissions per year
Production will however increase significantly in the coming years as large expansions of the factory are planned.
From Gothenburg enough engines and transmissions for a day of production are loaded unto trucks bound for Trollhรคttan
Currently, hundreds of engines and transmissions are transported every day. This is a very valuable cargo as a result.
It is in Trollhรคttan that Saab produces its cars. In recent years, Saabs automobile activities have more important for the company itself and our country as a whole.
Saabs cars not only make us less dependent on foreign imports, they also constitute valuable exports to countries all over the world- including America
Saabs car production has now reached a point that must be considered significant.
As the cars have been developed and improved the rate of production has increased to about 30,000 cars every year.
As a result of the 1959 inauguration of the new factory in Trollhรคttan and the expansion of the Gothenburg factory it will soon be possible for Saab to produce over 60,000 cars per year.
In contrast to many other car manufacturers, Saab manufactures the car’s bodies in its own workshops.
Our cars are also pressed in extra thick steel to make the cars as safe as possible
From the workshops the bodies are transported into the new factory
Corrosion protection is applied in a fully automated process. Then the bodies are transported to the paint shop.
Before the final coat of paint is put on, a protective layer is applied that greatly increases the longevity of the car.
After cleaning, the bodies get their final coat of paint and are thereafter transported to the assembly line.
The car is soon a complete - a car with airplane qualities
In the extensive quality control evaluations the car’s waterproofing is tested, among other things.
Currently, Saab produces three different models
The practical station 7-seater wagon, Saab 95 ...
the elegant 5-seater Saab 96 ...
and finally the exclusive, sporty model Saab Granturismo with more power and special equipment as standard
Even if the Saab 96 already has been tested for production, rigorous tests continue to ensure build quality.
One of the tests involves a man lying on the bonnet, peeking into the engine compartment through a plastic window as the car drives through a puddle - checking to make sure no water enters.
SAAB - A company for the future
Chevy Bolt Review - Chevy Is Headed in the Right Direction but It's No Tesla
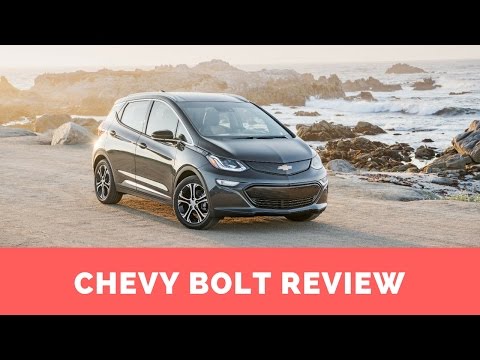
Teslanomics with Ben Sullins:
Decoding and Understanding Vehicle Identification Numbers / VIN's

1A Auto Parts:
2007-2018 Silverado 1500 Power Stop OE Replacement Brake Rotor & Pad Kit - Front Review & Install

AmericanTrucks Chevy & GMC:
Hey, guys.
Adam here with americantrucks.com.
Today we're taking a closer look at and installing
the Power Stop OE Replacement Front Brake
Pad and Rotor Kit available for the '07 to
'18 Silverado 1500.
You should be checking this out for your own
Silverado if you're in need of a new set of
rotors and pads and you're not looking to
spend big bucks on something with all the
bells and whistles like a drilled and slotted
rotor or a fancy pad.
This is literally the exact same quality in
the exact same setup that you got from your
truck off the factory line just made from
Power Stop.
This kit includes a G3000 casting grade rotor
manufacturing process, you're getting the
same OE quality rotor going right into the
factory location using your factory calipers.
The pads are gonna have a 100% dust-free,
brake noise-free, ceramic pads.
So, they're high quality and again, just the
same quality as your factory one which is
really actually what a lot of guys look for.
A lot of guys aren't really in the market
for some of those aftermarket fancy stuff.
For right around 100 bucks, you get your entire
front kit for replacements on your braking
assembly.
Now, as we know the trucks as they get older,
they're gonna need brake jobs, they're gonna
need new rotors.
And if you're replacing your brake pad, it's
always a good idea to do the rotor at the
same time.
When you're using factory pads and factory
rotors, they break-in together and have the
same kind of grooves.
So, if you replace pads and not rotors, the
old rotors are gonna create the same grooves
on your pads and wear them out a lot faster.
So, anytime you're replacing one, you really
wanna replace them both.
And with this kit, you're getting all of that
together conveniently for the front end.
Anybody can tackle it in the driveway at home
with a little bit of patience and following
directions.
Whenever you're doing pads and brakes or anything
really inside that wheel well, you wanna make
sure you're using extreme caution, you wanna
know what you're doing.
Read the directions because messing with brake
assemblies it can be pretty dangerous if not
done correctly.
So, I'm gonna show you every step of the process
to make sure that you can do it in the driveway
at home.
There are a couple of specialty tools you're
going to need and I'll walk you through the
entire tool list.
I recommend some anti-seize lubricant which
is gonna make it a little easier to make sure
there's no squeaking, no squealing when the
pads contact the caliper itself.
You're also gonna need a torque wrench and
I'd recommend a breaker bar or a larger ratchet.
Something to give you a little bit more leverage
to break those caliper brackets loose.
After a while, it can get a little rusty and
really seized up in there so having something
to give you some more leverage to break them
loose is gonna go a long way.
Now, the install is gonna get two out of three
wrenches on our difficulty meter.
I'd recommend having about three hours on
deck from start to finish at the front end.
If you have more experience, it might take
you a little bit of less time.
Because we're not replacing the caliper itself,
we don't have to bleed the brakes which is
one thing off of our minds we don't have to
worry about.
Without me rambling anymore, I'm gonna show
you every step.
Let's get to it.
Tools used in this install include an impact
gun, 18-millimeter deep socket, 18-millimeter
swivel socket, 19-millimeter deep socket,
T27 Torx bit, dual-piston caliper tool, anti-seize
lubricant or brake lubricant, half-inch ratchet,
pry bar, breaker bar, and a torque wrench.
All right, guys, first step, of course, is
to get your truck up in the air safely whether
that be on the ground on jack stands.
Make sure you're using your floor jack as
added support in case of a jack stand failure.
You just wanna be using extreme caution when
jacking up your truck.
Get your wheel off.
As you can see, we've already done that.
Grab a 19-millimeter socket, we're gonna remove
the two bolts holding your caliper to the
caliper bracket.
There's one at the top and one here at the
bottom.
All right.
So, with those two bolts out of the way, you
should be able to pull your caliper off.
Now, because it's under some pressure in there,
you might need a pry bar.
You're gonna pry from the top, from the bottom,
and just go back and forth until it works
its way off, and you pull it straight back.
If you are unable to pop the caliper off of
the caliper brackets, you can skip that and
go straight for the two bolts that hold the
entire assembly on.
We're gonna take the bracket off anyway.
I like to take the caliper off first.
If you're having trouble with that, you can
just take the whole thing off.
All right.
Once you get this off, you wanna place it
up here on your upper control arm safely so
it doesn't hang down and put pressure on the
brake line.
All right.
So, at this point, if you're able to you can
pop your brake pads out.
This one here is a little tight.
This one here is just a little bit of movement
so I'm gonna pop them out with the caliper
bracket altogether.
All right.
Since they're on there pretty tight, we don't
have enough torque on our impact gun.
I'm gonna a half-inch ratchet with an 18 socket
just to break them loose.
All right.
So, we got those broken loose.
Now, we can get them off.
All right.
With those two bolts out of the way, we can
pop our bracket off and set it aside.
All right.
Next step we can pop our rotor off since we
are replacing our rotors.
We're gonna use a T27 Torx bit to get this
one little screw off.
A T30 will be a little more snug but this
is what we got.
Pop that off and now we can take our rotor
off.
All right.
So, we got our factory rotor and our pads
off of our '14 Silverado 1500 behind me.
I wanna take you through some of the similarities
and differences between the two kits.
And I got to be honest with you, guys, there
really aren't any differences between the
two.
The Power Stop kit we have here on my right
is just a straight-up OE replacement.
This is a direct replacement for your factory
solid rotors and your factory ceramic pads.
These rotors here from the factory are G3000
grade casting rotor manufacturing process
going into those rotors.
They're also 100% mill balanced and non-directional.
Same exact quality here on the Power Stop.
Your new pads are 100% ceramic pads.
They also offer a noise-free braking experience
so you don't get any squeaks or squealing.
And really, guys, as you can see our factory
pads really do have some meat still left on
them but a huge difference between those and
our new pads here, these are 100% fresh.
Our rotor is looking a little worse for wear,
we're seeing a little bit of rust around the
edges, it's about time we upgrade that to
our new replacement.
And if your brakes are looking a little worse
for wear as well, this is a good thing to
get.
If you're not looking for anything fancy you're
not looking for the all bells and whistles
that you'd get from a drilled and slotted
rotor, any kind of fancy pad, this is really,
again, direct replacement.
So, what we're gonna do is use our new stainless
steel hardware to replace our factory hardware
inside of our caliper.
We wanna put the new clips in.
It's always a good idea to replace those when
you're going through this process.
They get a little rusted, a little worn out
so we're gonna throw those guys in.
We'll add a little brake lubricant on the
inside to prevent any metal on metal squealing.
We'll lube up the back of our new pads, we'll
stick them in the caliper bracket and start
replacing our stuff.
These are gonna need a caliper C-clamp.
You'll have to depress or decompress the caliper
pistons, in this case, our dual-piston caliper
to make room for your new pads.
Because your calipers are under so much pressure
and when you're hitting those brakes, it clamps
in.
It gets stuck in there when your pads are
not being pressed in.
So, what we need to do is decompress that,
put on our new pads, and then we'll work from
there.
So, what we're gonna do first is use our new
hardware and install our pads.
All right.
Now, what we can do is look at our factory
bracket.
We're gonna pop off the metal clips that were
holding on those pads.
What you can do here is push straight out
on the top and it disconnects.
You wanna take note of how they were seated
in there.
Grab the clips in the kit that are the exact
same style.
There are a couple of different versions of
these clips in the kit.
Some have this tab facing backwards, some
are facing forward.
Grab the forward-facing ones.
They're gonna sit right in here on our driver
side bracket.
So, we're gonna pop our old guy out.
And if you have any rust in here, you wanna
make sure you're cleaning that out.
Ours is looking pretty good actually so we're
just gonna pop in our new guys.
These new ones will seat right in there and
you're just gonna push and they snap right
into place.
And we feel that click and now they're secured.
Same thing on the other side.
Now what we can do is put our old stuff aside
and grab our pads.
Now, the pads are gonna seat in there a very
specific way.
You wanna make sure they're seating in with
that curve with the ceramic pad portion on
the inside of the bracket.
Now, before we actually insert this, what
I wanna do is first off try to avoid touching
the surface of the ceramic pad.
You don't wanna get any grease or oil on there.
What you wanna do is look at the back and
we're gonna apply a little bit of anti-seize
or brake pad lubricant.
We're just gonna rub that on the back pad
here.
I'm also gonna rub it on the sides that are
gonna contact the metal on the inside of the
bracket.
We just wanna avoid any excess squealing and
the anti-seize is a good way to go.
I'm gonna pop these gloves off, throw some
some latex gloves on which I'd recommend having
on deck just so you don't get lubricant everywhere.
That's definitely not what you want.
We're gonna apply that.
Now, when you are applying it, guys, you wanna
be careful.
You don't wanna put any anti-seize on the
surface of the brake pad and you don't wanna
get any of it on the surface of the rotor.
It kind of defeats the purpose of braking.
You don't wanna lubricate it, you wanna create
more friction not less.
So, what we wanna do is lubricate that up.
I'm gonna set this down, take my gloves off
and we'll be right back.
All right.
So, what I'm gonna do here is grab our anti-seize,
I'm gonna put a little bit on my finger and
just cover the back end of the plating here
on our caliper.
I'm also gonna grab a little bit, put a little
bit around the edges where it's gonna contact
the metal plating.
It's also not a bad idea to just throw a little
bit on the inside there.
All right.
So, as you can see, this pad here is completely
curved on the bottom.
The curved section is gonna go over the curved
section of the bracket.
The one with the flat section is gonna go
over the flat section of the bracket.
It's pretty straightforward.
So, this is gonna slide right in here.
I'm gonna line it up with the ends of the
brackets and seat it all the way in forward.
Do the same thing with the other one.
You can see this brake pad has a flat section,
that's gonna go on the back flat portion.
All right.
So, now we can grab a rotor and we're going
to install this onto our hub.
What you wanna do is line up the threaded
hole in the rotor to the threaded hole on
the hub.
All right.
So, now what we can do is put in that factory
Torx screw, Torx bolt and just tighten them
in my hands.
Now, we can grab our socket.
All right.
Now, we can drop our caliper bracket in place
with our pads.
Now, what we have to do is line up the factory
bracket with the factory holes.
Grab the 18-millimeter bolt and we're gonna
put it in lightly by hand just threading it
through just to hold it in place.
All right.
Do the same thing for the top.
You're gonna make sure those threads are catching
first before you let go.
All right.
Looking good.
Tighten them down.
I'm gonna get them nice and snug and then
go back with a torque wrench.
What you wanna do is grab a torque wrench
and torque the two bolts down that are holding
your caliper bracket to the knuckle to 170
foot-pounds.
So, now what we have to do is take our caliper,
we're gonna flip it upside down.
Just rest it right about here.
Now, because our new pads are thicker, this
space is no longer big enough to fit over
the new pads.
It got really used to the thinner pads, the
older pads once were used because it compresses
in.
So, what you have to do is push these two
pistons back.
Basically, what you're gonna do is just pull
this trigger a bunch of times and this bracket
here is gonna compress those two pistons in
just like that.
We're gonna push.
You can see it compressing in all the way
back.
Perfect.
Release.
And now it should fit over the brake pads.
So, now we can rest this over the pads and
line those up to the holes just like that.
Grab the factory bolts and put them through.
All right.
Now, we can grab our socket and tighten them
down.
And this is a 19-millimeter socket.
All right.
You don't really need a torque wrench for
this one, you're just gonna get them really
nice and snug with your impact gun.
So, really at this point, you're just pushing
the brake pedal in.
You'll feel it go a little bit further in
the first time.
But as you pump it five or six times, you
feel it gets stiffer and stiffer until it
feels normal.
Now, you can repeat on the other side.
Well, guys, that's gonna wrap up my review
and install for the Power Stop OE Replacement
Brake Pad and Rotor Combo Kit available for
the front end of all '07 to '18 Silverado
1500s.
If you want, you can get your Power Stop replacements
right here at americantrucks.com.
GM Lied To The Public And To Trump About Where Chevrolet Cruze Sedans Sold In The USA Are Assembled
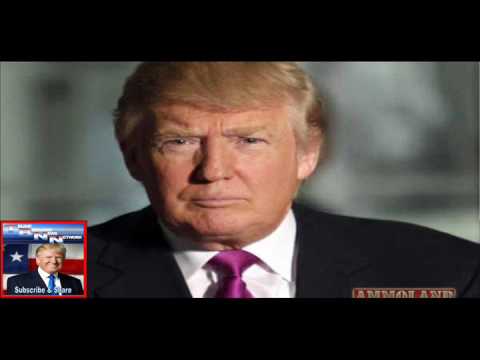
Trump Breaking News Network:
GM Lied To The Public And To Trump About Where
Chevrolet Cruze Sedans Sold In The USA Are
Assembled.
by Tyler Durden.
On Tuesday, president-elect Trump tweeted
about General Motors, stating the GM was building
its Chevrolet Cruze in Mexico, importing them
to the US tax-free, and selling them at US
car dealers:
GM quickly denied Trump�s tweet, and in
a press release that same day, the company
claimed that all Cruze sedans sold in the
US are �built in GM�s assembly plant in
Lordstown, Ohio�, and that GM builds the
Cruze hatchback for global markets in Mexico,
with only a small percentage being sold in
the US�..
�and the MSM and other liberal outlets were
quick to pounce on GM�s statement, using
it to slander the president-elect.
US News, ABC News, and many others, including
the Wall Street Journal, all published articles
containing the information in GM�s press
release.
US News went out of its way to post a clickbait
headline which alluded to �the truth�
about Trump�s tweet, with the following
quotation:
General Motors Company (ticker: GM) is pushing
back after President-elect Donald Trump early-morning
Twitter attack, in which the incoming president
took aim at GM for making its Chevrolet Cruze
in Mexico and shipping them tax-free to the
U.S. for sale.
That�s not the full story, says GM.
�General Motors manufacturers the Chevrolet
Cruze sedan in Lordstown, Ohio,� a General
Motos spokesman told U.S. News & World Report
in a statement Tuesday.
�All Chevrolet Cruze sedans sold in the
U.S. are built in GM�s assembly plant in
Lordstown, Ohio.�
GM says it also builds the Cruze hatchback
in Mexico to sell in global markets, and only
a �small number� of those are sold in
the U.S.
It did not clarify the number.
The hatchback model went on sale in the U.S.
for the first time this fall.
Of course, the liberal think-tanks like Politifact,
ThinkProgress, GOOD, Addicting Info, Salon
(whom I refuse to link to), and countless
others got in on the act.
Addicting Info in particular went out of its
way to imply that Trump was wrong, and dangerously
so:
But as a result of Trump�s accusations and
threats General Motors� stock price tumbled
briefly and then recovered.
Keep in mind that General Motors was nearly
wiped out of existence at the beginning of
the Great Recession, which would have cost
thousands of Americans their jobs.
Trump�s attack on General Motors could have
harmed the company in a way that would have
harmed American workers he the stock price
fallen more than it did.
Trump just flat-out lied to the American people
and got busted for it by General Motors.
Next time Trump decides to attack an American
company he should do his homework first and
then look in the mirror because his company
has most of their products manufactured in
China and Mexico, which make Trump the biggest
hypocrite in America.
It appears that in the MSM�s rush to fact-check
Trump and call him hypocritical, no media
outlet bothered to fact-check GM as well.
So, who did the fact-checking work that the
MSM didn�t bother doing?
Auto enthusiast and Twitter user E.W. Niedermeyer,
that�s who.
Niedermeyer brought the GM and Trump saga
up on Thursday, January 5th in a series of
tweets that began innocently enough�
�Niedermeyer quickly got to the nitty-gritty
of his argument, noting the the VIN sequence
(3G1) used at the beginning of GM cars made
in Mexico�
�and finally, Niedermeyer provided evidence
on where the autos sold in the US were built:
Think about that for a second � GM is selling
Cruze sedans manufactured in Mexico, in the
same Ohio town that builds Cruze sedans.
And at the same time, GM is brazen enough
to say it doesn�t sell Cruze sedans built
in Mexico in the US, saying all Cruze sedans
in US dealerships are built in its Lordstown,
Ohio plant.
And GM did so in the face of the president-elect
of the United States accusing the company
of building Cruze sedans in Mexico, shipping
them to America tax-free, and selling them
in your local dealerships.
Niedermeyer�s entire tweet thread can be
viewed here.
Neidermeyer provides ample evidence demonstrating
the truth about where GM Cruze sedans sold
in the US are built.
Feel free to check the VIN numbers on your
local Chevy dealer�s Cruze inventory, and
see where they were built for yourself.
GM was caught red-handed lying to the public
and to Trump, and we might never have known
if it weren�t for everyday people like Niedermeyer.
It is crazy enough to wrap your head around;
a regular guy did the fact checking the MSM
never bothered to do.
The MSM took GM�s word as gospel in their
rush to criticize Trump, without bothering
to check if GM was just lying to save its
own skin.
If you think GM is somehow more credible than
Trump, recall that this isn�t exactly the
first time the auto maker has been caught
lying.
In fact, they have been caught lying again,
and again, and again.
Sometimes their lies result in people losing
their lives.
They have been caught lying so many times,
it would be impossible to list them all here.
But the MSM gleefully took GM at their word,
using any chance it could get to refer to
the president-elect as a dangerous, reckless
liar, when a simple fact-check has shown GM
was falsifying the truth, not Trump.
Allow this revelation to resonate in your
head for a second, and keep it in the back
of your mind next time the mainstream media
tells you Trump is a dangerous liar and/or
hypocrite in his latest tweet.
Because you just might be the fact-checker
that gets the last laugh, right alongside
Trump himself.
As a quick follow-up, The Daily Caller is
reporting that GM effectively confirmed the
analysis above.
But don't worry because all of the imports
in 2016 were just a 1x thing to "supplement
the launch of the Cruze" at it's Ohio plant.
Chevrolet

Audiopedia:
Morgan Motor Company: The Most Honest Car Factory in the World - /DRIVEN
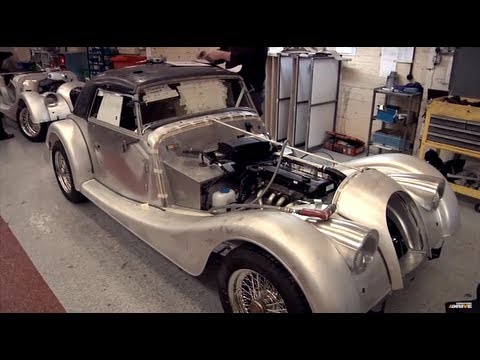
THE DRIVE:
[ENGINE REVVING]
[MUSIC PLAYING]
JF MUSIAL: What you're about to
see is the most authentic,
honest car factory
in the world.
Welcome to the Morgan
Motor Company.
Unlike other factory tours that
take weeks of phone calls
and emails just to orchestrate,
Morgan is an open book.
Every other car factory we've
been to, we're always ushered
past secret rooms that hold
future designs and technology
worth millions of dollars.
This Malvern, England based
workshop holds no secrets.
All you'll find here are happy
designers, craftsmen and
women, the smell of wood,
glue, leather.
And did I say wood?
So what do you need to know
about this place?
Well, this is the oldest car
company in the world owned by
a single family.
Their designs, not much
different from
five decades ago.
They produce a three-wheeled
car called,
well, the three wheeler.
And simply put, this is just
the coolest [BLEEP]
place you'll ever visit
as a car enthusiast.
And what better person to give
us a tour than a Morgan?
A Mr. Charles Morgan.
So, Charles, where
are we right now?
CHARLES MORGAN: Right,
well, this is
where it starts, really.
This is the start of the
Morgan assembly line.
It all starts with the chassis,
of course, that we
actually import in from
Birmingham, which is only
about 30 miles north of us.
But this is built for
a [INAUDIBLE]
shape to our designs,
obviously.
It's designed on a
CAD [INAUDIBLE].
And as I said, it's cohesively
bonded aluminium.
You've got what is the same
principle as the racing cars.
In other words, what I'm saying
is, the chassis does
all the work.
It provides all the stiffness.
It provides all of the mounting
points for the engine
and the gear box and
the power train.
And we even, of course,
fit the fuel tank.
We fit all the electric wiring,
which is neatly hidden
inside the chassis.
And you can actually
start the car.
You can drive it as a chassis.
It's not actually driven.
But we do run it.
And of course we run it because
we have a quality
check that is demanded
by BMW or by one
of our engine suppliers.
And that means you go through
all the diagnostic checks on
the engine.
And what I quite like about
that, doing it as a chassis,
is that everything is visible.
So if there are any leaks, or
if there is any problems at
all, it's all accessible
to put right.
And that's particularly
pleasant if you're an
electrical engineer, for
example, because modern wiring
[INAUDIBLE] are very,
very complicated.
What happens in this e-box,
there's actually five
computers, I think,
in this car.
This is actually the 4.8 liter
BMW, which it's still a
current engine, but they've
built it especially for us.
And the reason they do that is
they've gone twin turbo 4.4
liter to keep the
emissions down.
But actually, the 4.8 in this
car, because it only weighs,
less than 2,000 pounds--
it's about 1,150 kilos.
This car is ultra light.
So actually, the emissions
are very low anyway.
So we didn't need to go to the
complications of the twin turbos.
But this is the diagnostic
check equipment, so that
allows us to run
the engine up.
-Are you sure that doesn't pick
up any Nazi frequencies?
[LAUGHTER]
CHARLES MORGAN: It's an early
mobile phone actually.
I think one of the reasons why
BMW quite like working with
us, to be honest, is that most
of their cars are still
[INAUDIBLE].
And they tend to be a lot
heavier than an aluminium car.
So the engineers--
I'm not talking about the
marketing people here, but the
engineers quite enjoy seeing
their product in our
lightweight frame.
Dr. Schmidt-- who's left
unfortunately, I think he's
gone to Ford-- but he was
the head of engine
power train at BMW.
And he got out one of the
earlier versions of this and
said, at last, Charles,
I can feel my engine.
Because normally
it's so quiet.
[MUSIC PLAYING]
JF MUSIAL: I wouldn't be able
to do a full episode on the
history of Morgan.
It would just take too long.
But here's what you
need to know.
The roots of the company come
from HFS Morgan, with a basic
vehicle formula--
Powerful motorcycle motors,
light chassis, simple,
resourceful, and fun.
And for Malvern, where every
road somehow leads up a
mountain, that's especially
useful.
So let's start off with--
what is this thing?
I've seen it before, but I
have no idea what it is.
JONATHAN WELLS: OK, well, this
is our 2009 life car concept
vehicle, really.
And this was a car that featured
a hydrogen fuel cell
platform underneath it.
So it's a completely
zero emissions car.
It was a great advertisement
for the company, because
people see a zero emissions car,
and they go, wow, Morgan,
a sports car maker is building
something very
environmentally friendly.
But then you actually to get
into Morgan and the brand, and
it does a lot more.
When you realize that all the
materials in this car are
locally sourced.
And the factory itself isn't
using big machinery, and it's
hand crafting these vehicles.
It's a low energy manufacture.
The car is very lightweight.
You've got all these other
fantastic environmentally
friendly accreditations that
they're adding to it.
So although it is a zero
emissions vehicle, every
Morgan is actually very
environmentally friendly.
They have a long life span.
They're kept for a long
period of time.
So, it was just a testament to
the way in which we build cars
considerably.
JF MUSIAL: I think the one thing
that we all notice when
we first come in here
is the smell.
CHARLES MORGAN: Yes, this
is the wood shop.
This is very unusual to
find a wood shop like
this in a car factory.
You'll find veneers in a luxury
car factory, but you
won't find guys putting together
solid hard wood
that's this grand.
Obviously these are
the back presses.
When you laminate some wood--
this is really heavy-- ah,
I can't pick it up.
But when you laminate wood,
obviously you put the grain in
the different directions, and
then you bond them together.
And of course, you want to take
all the air out of it
that you can to stop the air
bubbles in the glue, so that
creates a bonded laminate.
And that's a very strong
component.
And of course, it's got
a lot of spring in it.
And it seems to last forever.
That's partly why we use wood.
We also use wood, to be
honest, because it's
environmentally correct.
Because it encourages people
to plant forestry.
And it's the young trees
that clean the air.
So it's our, if you'd like,
bit of greenness too.
But we're actually using wood
in sustainable forestries
that's being kept going by
people who use wood.
But I suppose the other thing
is it gives us a unique
proposition.
And these days, basically,
there's so much competition in
the car industry, we
want to maintain
something that's very Morgan.
Something that's
very different.
And as you said, the smell's
very nice, too.
The 1950s.
Plus Morgan plus four coupe.
And we've got it here just to
show that we can actually
build the cars and keep the
cars going on the road.
For instance, Morgan probably
has got about 30,000 or 40,000
cars around the world.
And they do say that a
Morgan never dies.
The wood--
it's not in brilliant
condition, is it?
But the fact is that
you can replace it.
So basically, what people tend
to do with Morgans, is that
they re-chassis them.
They re-body them.
And they keep them going with
components, which again, is
very, very good from the
environmental point of view.
Because ideally, what you want
to do is produce a product
that generation after
generation, like a watch, is
going to want to keep going.
That's very much part
of our philosophy.
Now, one person definitely is
responsible for a chassis and
for a wood frame.
So if you like that,
that gives the
ownership to the operator.
And he signs it off.
He could actually sign it.
Sometimes they do.
They sign it.
But I think it's very important
to recognize that a
car is a combination.
It's not one person that build
the whole car, but it's a
combination of different people
who actually are really
skilled in their own
particular area.
The wood's ash.
It's English.
It grows fairly straight.
Comes from England or Europe.
Not America.
It's faster growing
in America, but
it's a slow grow here.
What's good about
it is the grade.
You don't tend to get too many
knots in it, and so you can
use a lot of it.
And it grows fairly straight,
whereas oak tends to go in
lots of different directions.
But it's the same material
as a handle of a
cricket bat, for instance.
It absorbs shock really well.
In the old days, in the Italian
factories, they have
this thing called Superleggera,
and that was the
aluminum body.
And then you added some
tubular steel frame
underneath.
And in a sense, this is
exactly the same.
This is the structure underneath
the aluminum body
of the three wheeler.
Under this, of course, is
a big tubular chassis.
Yeah, but this if you like, is
just a way of keeping the
aluminum taut and acting as
a little bit of a cushion
between the chassis
and the body.
The problem with Superleggera,
of course, is that it was
steel against aluminum.
So of course the aluminum
reacts with
the steel and corrodes.
We don't have that problem
with the wood.
So to an extent, this is
Morgan Superleggera.
Without the problems.
When you actually treat the
wood, and obviously this is to
a certain extent, how much
work you want to put in.
A bit like a favorite
pair of shoes.
They tend to get better
with age.
JF MUSIAL: Yeah.
CHARLES MORGAN: And
so will wood.
And it will look better and
better and better the more you
rub it and polish it.
This is obviously [INAUDIBLE].
So I prefer this style of luxury
interior to veneers.
Veneers are an acquired
taste, really.
Veneered cigar boxes and
all that kind of thing.
This is more honest, I think.
Proper real wood.
And of course, what you get
here is you get the same
thing, where you get every bit
of wood slightly different.
So you've got a very personal
product out of wood.
These jigs are slightly
fascinating.
They've been here since
the war, I suppose.
JF MUSIAL: What is
the jig for?
CHARLES MORGAN: Well, this
is the real [INAUDIBLE]
for one of the traditional
cars.
JF MUSIAL: Oh, cool.
CHARLES MORGAN: And as you see,
it's just three bits of
ash with the grain going
a different direction.
JF MUSIAL: So you've got the
vacuum stuff over there.
That's the modern
version of this?
CHARLES MORGAN: Yes.
This is just sheer
brute force.
JF MUSIAL: And how long are
they staying in here for?
CHARLES MORGAN: Half a day.
Six hours.
JF MUSIAL: Cool.
It's very cool.
JONATHAN WELLS: But what I
brought to the design team
essentially is 3D surfacing.
So Matt would sketch the ideas
out, and I'd draw with him.
And then we needed some way
of relating these concept
sketches and aesthetic design
training to the way we build
cars in the shop floor.
So my job would be to take the
sketches and model these in
3D, sometimes in clay as well,
but mainly in 3D on the
computer screen.
We'd apply textures and
materials and colors to this,
and visualize exactly
what this car is
going to look like.
Show this to Charles, and say,
here you go, Charles, this is
your car in 3D.
Once we have the sign-off, we
would then chop this car up on
the screen, take out some
printed plots to the wood
shop, they would make this out
of wood, and then the plan
would be to hand craft
this entire car.
So everything you see here is
hand beaten from a flat sheet
of aluminum.
JF MUSIAL: It's amazing you've
from modern technology back to
old vintage technology.
JONATHAN WELLS: Exactly, yeah.
[MUSIC PLAYING]
-And that brings up an
interesting point.
Every corner you turn your
smell something new and
wonderful, like a chef walking
into a fresh produce market.
But not only that, you start
looking at the faces.
Less than 200 people work
in these work shops.
Everyone from designers
to wood craftsman.
It's a close-knit family.
Men and women with 40 years of
experience between these walls
training young teenagers.
There are no instruction books,
no Volkswagen era
just-in-time logistic systems.
Everything is taught by word
of mouth with the hands of
experience.
And despite the archaic
methods,
it's all just working.
It will continue to work for
years to come, even as they
ramp up daily production.
CHARLES MORGAN: So once you've
got the wood frame, then we
cover it in aluminum.
And the panels are a combination
of pre-formed and
literally hand assembled.
So what you'll see is
somebody actually
wiring the edge of this.
So he's turning it around
and putting a--
JF MUSIAL: It's all hand done?
CHARLES MORGAN: Hand
done, yeah.
This is actually a 1950s
or 1960s body.
It's a lot narrower.
People were smaller
in the old days.
JF MUSIAL: Seems
that way, yes.
CHARLES MORGAN: Cars
were smaller, but
they're all very light.
Once you've--
JF MUSIAL: Whoa!
Could we both pick it up?
CHARLES MORGAN: Yeah,
of course.
That's the whole car.
JF MUSIAL: That's incredible.
CHARLES MORGAN:This, again, is
about a six-hour process to
assemble the aluminum panel.
We tend to have a half day cycle
throughout the factory,
so that things move
on every half--
I think you'll still find
the affordable cars,
they're using aluminum.
The new Jaguar F type is very
much an aluminum car.
And we pioneered that technology
on the Aero, so
yes, we're not perhaps
pathfinders anymore, but we
were pioneers then.
The trouble with carbon fibers
is there's a very
short supply of it.
It's mostly wanted by the
aircraft industry.
So the price has gone
through the roof.
So it's really only super
car territory.
And our buyers are not
necessarily people who want to
pay 500,000 pounds for a car.
JONATHAN WELLS: There's certain
elements that have a
nod to a more classic
era of motoring.
And that's what's nice
about a Morgan.
Morgan doesn't conform to
generic car design.
It doesn't follow
any rule book.
Nowadays, car design can be
quite constricted by the rules
and regulations and positions
of certain parts of the car.
We try not to get too
blinded by that.
We like the proportion
of the Morgan car.
The wind line in vehicles like
this, we try to add a bit more
tension to it, and strengthen
it a bit, and give it a bit
more stance and purpose.
But, as you say, that classic
form is very much there.
It's the British Coke
bottle proportion on
the side of the car.
But, as I mentioned, some of
these lines are sped up a
great deal.
There's a lot more sharp edges,
which break the air
away cleaner, and improve the
aerodynamics, while staying
true to what we can achieve
with the actual materials.
CHARLES MORGAN: So, this
is our paint shop.
As I say, once the car's
disassembled,
they all come in here.
And each component is painted.
We've actually got two paint
shops because the constraints
on our production system
is paint, really.
It's the slowest process,
is baking the paint.
JF MUSIAL: Waiting.
CHARLES MORGAN: And waiting
for it to dry.
JONATHAN WELLS: In the
development department,
there's 10 of us.
Very closely tight knit team.
JF MUSIAL: Are you
all in the same--
JONATHAN WELLS: Literally
all in the same room.
And everybody is a genius and
a specialist in their own
right that gets involved with
lots of different things.
And as you mentioned, you do
have to conform to things like
harmonization, and get
this passed off.
In a lot of companies, the
design may happen, and then
enters the next division
where you can't do this
and can't do that.
And something's lost.
And then it moves on again,
and the material engineers
can't quite work with this,
so something else is lost.
And you end up with a
fairly generic form.
But for us, when we're drawing
and we're sketching, I've got
harmonization here looking over
my shoulder going, oh
those headlights need
to be a bit higher.
So I scrap that drawing, and
I work on the next thing.
And arguably, that could
compromise the design in some
instances, but what we find is
when you do hit the nail on
the head, and you get something
that works, really
exciting concept sketch, and
harmonization are happy
straight away.
And so are the material
engineers.
So is everyone else.
That idea has got more chance to
make it all the way to the
road, to the end user,
with that same
excitement and drama.
I think essentially over the
last 10 years, it's been a
roller coaster at Morgan.
Cars like the Aero have come
along and shown people that
you can build super cars
with this DNA.
And when you are building
vehicles, with those
performance figures like the
Aeros-- and even the three
wheeler on the other end the
spectrum-- do have, you do
have to consider a lot more
suspension dynamics, and
aerodynamics, and all
sorts of stuff.
These tests are very
expensive.
Wind tunnels are
very expensive.
So small companies like us are
encouraged, really, to start
using a lot of onscreen
simulation.
So we do.
We run every single CAD model
through onscreen CFD.
CHARLES MORGAN: Oh,
nice and quiet.
JF MUSIAL: Yes.
CHARLES MORGAN: We're now
smelling cow or leather, as we
would call it.
But no, essentially as I say,
the assembly goes back
together, and then we start to
trim the inside of the car.
And this is where you see the
different specifications that
a customer wants coming out.
We actually use Scottish
leather.
The cows are from Scotland.
I think there's less barbed wire
out there, so they don't
scratch them.
But no seriously, that's
the reason, actually.
And--
JONATHAN WELLS: We had the idea
for three wheeler, and we
started sketching it.
And 18 months later, we're all
in the workshop doing a
48-hour stint building the
things up ourselves, and
seeing this design
come to life.
And it's at the Geneva
Motor Show.
A matter of a few months later,
the first cars are on
the road going to production.
So from a sketch to a full
complete production car on the
road, you're talking less than
two years, which is no time
really, compared to
other companies.
JF MUSIAL: Comapred to the
big manufacturers.
The Americans, the Germans, the
Japanese, who spend six,
seven, eight years designing--
JONATHAN WELLS: I think that's
testament to the
way in which we work.
And the way the factory and
development and technology are
all united in this pot.
CHARLES MORGAN: This is
basically where all the cars
come after they've
been road tested.
JF MUSIAL: Every car
gets road tested?
CHARLES MORGAN: Every car
gets road tested.
And then it comes in here.
And this is the detailing,
if you like.
So it enables us to really,
really inspect the paint work.
Essentially, each car will
spend about half a day in
here, get a thorough inspection,
and then be passed
off for quality control.
JF MUSIAL: Who's the final
person that signs off on a car
going to the customer?
CHARLES MORGAN: One
of these guys.
JF MUSIAL: Each person
is assigned a
car and sign it off?
They go through a checklist
of things?
CHARLES MORGAN: Absolutely.
JONATHAN WELLS: I think Morgan
design is uncompromised.
I think it's excitement
and fun.
It's happiness.
I think people see a Morgan, and
it makes them feel happy.
There's no pretentiousness,
there's no arrogance.
It's a very honest design,
which is challenging,
uncompromised, and there's
a lot of stories to it.
There's a lot of story.
There's a lot of meat to
talk about in the pub,
when you pull up.
CHARLES MORGAN: Morgan's link
with motor racing, really, is
that we've used it
as a test bed.
So essentially, we feel that if
a car performs well on the
track, then it's going
to perform
quite well on the road.
There are now, of course,
test tracks as well.
And that's another thing.
The German manufacturers will
tell you that if you can drive
a car 200 miles an hour, it's
going to be really quite good
at 100 miles an hour.
So there's an element
of that in it.
But we also, of course, were one
of the first cars to have
a bonded aluminum chassis--
adhesively bonded aluminum.
Now, when I told that to my
father, he said, is that a
good idea, Charles?
I know we made those air fix
kits, but should we actually
make a car like that?
So we thought it would be quite
a good thing to test it
on the track first before some
poor owner actually finds out
that the bonding doesn't work.
Seriously though, Le Mans
is a 24-hour race.
So if a car lasts 24 hours at
the max at Le Mans, then it's
pretty sure it's going to be a
good road car as a chassis.
So we use the long distance
endurance racing and the GT
championships to bottom out
exactly what this chassis
would do under great stress
and under great strain.
And of course, you do put
bigger strain, because
typically a modern sticky
race tire will
pull 3G, perhaps more.
Whereas a road tire will
only ever go up to one
or a bit over one.
So you're putting a hell of
a lot more stress into the
components.
That's the main reason
we do motor racing.
Because it's all about
enjoyment when it
comes down to it.
We are about actually a car
factory, which provides people
with the experience of having
fun behind the wheel.
And I think you still
can in safety.
The super car world, and to a
certain extent, the racing
world has just gone out of--
it's gone completely out of
the possibilities of the
normal person, and
that's a shame.
Because to an extent, Morgan was
really about offering an
affordable way of going racing,
going into motor sport.
I've got some lovely stories.
In fact, one of them
is American.
The very first race at Sebring,
the 12 hours at Sebring.
And in fact, a competitor had
had his car blow up and was in
the pub, when a Morgan
owner arrived.
He'd only just bought his car.
I think it was a week old.
And he came to watch the race.
And the guy in the pub said, do
you want to enter with me?
Because my car's blown up.
And this poor bloke went,
well, all right.
So he ends up doing the race,
and they came 13th overall.
JF MUSIAL: With the car just
off the showroom floor.
That's cool.
CHARLES MORGAN: So that was the
philosophy behind Morgan,
really, was to provide a car
that without much work, you
could enter in a race
and do quite well.
Those days are certainly gone.
Well, internationally
they are.
But that doesn't mean to say
that we don't still believe in
that philosophy.
This is the top of the hill.
We have a very sophisticated
assembly line, actually.
It's gravity feed.
Well, it's only gravity feed
relatively recently because an
engineering guru came
around here.
And he said, gosh, this
is brilliant.
You've got this business of no
expensive equipment because
you just push the car
down the hill.
And I said, but the problem is
we're pushing them up the hill
at the moment.
So we've changed it now.
We are pushing them
down the hill.
How Brake Pads are Made
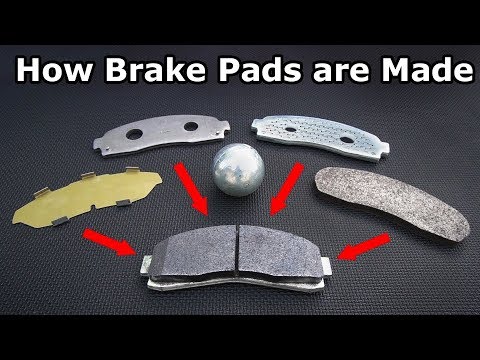
ChrisFix:
Hey guys ChrisFix here and today I need to replace the brakes on my truck
but instead of showing you how to replace brakes because i've done that multiple times with
In-depth how-to videos how to replace front brakes rear brakes drum brakes and on different makes and models
So instead of doing another how-to video on how to replace brake pads
We're gonna be doing something way cool. Today i'm gonna show you how brake pads are made
That's right. We're gonna go to the factory and we're literally going to make brake pads for my truck
It's one thing to go to the store and buy brake pads and install them. That's awesome
But it's a completely different thing to learn how these are made
The process that goes into it the testing and the different types of brake pads
So the issue I'm having you can see there's plenty of meat left on these brake pads
There's about half the life left on here
But the problem I'm having is you see all this rust in here and all this rust in here because the brake pads slide back
And forth in the brake caliper this part where it's painted
well
the paint gets rubbed away and
Shows bare metal and that bare metal will rust and this right now is getting seized into this brake caliper and the brake isn't budging
So although we have plenty of life left on our pads. We still have to replace them because they're getting rusted
So let's head out to the brake pad Factory and let me show you how brake pads are made
So while many brake pads today are made in China or India. I'm grabbing a flight from Newark, New Jersey and
Heading to Toronto Canada and here in Toronto
We're visiting new cap
the makers of
NRS brakes and their brake technology is used in om brake pads for big car companies like GM Ford Chrysler outtie and even Bugatti
And aftermarket companies like Brembo. So this is the real deal. We're about to see from start to finish how brake pads are made
It all starts right here in their engineering
Department in the United States alone. There are over 3,000 brake pad designs like this one
This is actually the one that fits in the caliper of my truck, which is this right here
Each brake pad has to be manufactured to strict tolerances
Because when you install brake pads in your car, they have to fit nice and tight
But still have room to move in the caliper, so it doesn't get stuck and to make sure each brake pad fits correctly
It all starts right here on the computer. This is the 3d model of my trucks brake caliper
And since we're making brake pads for the truck
All the precise measurements are going to be taken from this model and are going to be used to create the die
Which is going to stamp the brake pad backing plate, so it'll fit properly. So let's go and check out the stamping process
So we need a head over to the stamping facility for step two where we're gonna take raw steel and stamp the brake backing plate
And there is no shortage of steel on this factory each one of these coils weighs between three and five tons
And there are stacks of them to the ceiling
Look at all this deal and this steel is super important because it's gonna be turned into the backing plate
Which is the foundation of the brake pad so high-quality
Pickled and oiled steel is all this factory uses to make their brake pads
Let me show you why so all of these steel coils that you see in front of us are hot rolled
That means they're formed by heating them up and then rolling them out into shape after the steel is hot rolled
There are two things that could be done first. They could leave the steel as is and a scale a rust forms on top
That's called black steel
this steel isn't treated so that black that you see on here is all scale and impurities the
Positives of this are it's less expensive to produce than pickled an oiled steel
But the negatives are you have those impurities you have this scale you have this rust on here
And we didn't even make these into brake pads yet and on the other hand
We have pickled an oiled steel. The process of pickling steel is right after it's hot rolled
it's cleaned off with an
Acid so that you don't get that scale that you see with the black steel and then oiling it you could see there's a sheen
On here all they do is add oil so that it prevents it from rusting in the future
Now the negatives with pickled and oiled steel is it costs more than black steel?
But the positives are you're starting off with a cleaner rust and scale-free metal
Also, this is what the OEM requires brake pads be made of
So if you're making an OE brake pad you need to use pickled and oiled steel because it's a higher quality steel now
I'll show you the difference between pickled and oiled and black steel in the corrosion chamber a little bit later in the video
but for now know that this manufacturer only uses pickled and oiled steel now that you know
the significance of using pickled and oiled steel
Let's get our four ton steel coil and bring it to the press at the back of the press
The forklift operator has to put the coil into the loading bracket that another worker
Releases steel which rolls into the feeder and now the worker could feed the steel into the press
But since the steel was coiled up, it's curved and bent and bent steel can't be stamped
So first the steel has to travel through a series of rollers to be flattened out
So the brake pad backing plate could be stamped properly. Here's a closer. Look at what's happening?
The steel moves along the rollers which are positioned to make that steel flat
Then that flat steel comes out and gets fed directly into the press which has one last set of rollers to ensure. It's completely flat
Once that flattened steel makes it into the press the press applies up to 800 tons of pressure to stamp out a single backing plate
800 tons is like having the weight of
400 passenger cars stacked on top of each other pressing down on that single piece of steel. That's a lot of pressure
So after the brake pad backing plate gets stamped it slides down into one of two
Buckets and not into the main orange bin this two bucket design is so smart
And here's why they do it
Once one of the buckets gets full the worker closes the gate to that bucket and then the other bucket starts filling up he perceived
By grabbing a backing plate and blowing it off with some compressed air so we could visually inspect it
He's trained to look for anything that indicates the backing plate isn't being pressed correctly
If he sees an issue
He could shut the press and instead of contaminating the entire
orange bin of backing plates where there could be
Thousands of them already made he knows only the top two buckets have potentially bad backing plates
So this simple inspection prevents damaged backing plates from getting mixed in with the entire batch, which is very smart
All right. So check this out. We went from a coil of steel to this a freshly stamped backing plate
So at this point the backing plate is the correct shape and has all the holes and studs it needs
But what happens to the rest of the steel that isn't used in the backing plate on the side of the press all the extra?
steel that isn't part of the backing plate is also captured and
Recycled what you see here is scrap metal that comes from the area around the backing plate and this over here is the scrap metal
From cutting all the holes in the backing way
Nothing goes to waste here
That's good for both money savings and for being environmentally friendly all this metal will be melted down and reuse
Alright, and as you can see this containers almost filled as this finishes up now we can move on to the next step
so let's grab a backing plate and
Bring it to the Quality Control lab where the backing plate undergoes a full
Analysis to make sure each one has no flaws and will properly fit the caliper
So here's one of our backing plates and I'm gonna hand it over to the lab technician who's gonna place it on this high-tech scanner
The dimensional analysis scanner uses lights and cameras to precisely measure every part of the backing plate
It compares these measurements to OEM specifications in this case for my Mazda beat 3000 pickup truck if it isn't within the acceptable
Tolerances that'll come up on the screen as red and if it's good, it'll be green just like that. Perfect
Alright, and that is a pass now
Every single brake pad backing plate has a serial number stamped into it for complete traceability
This could be tracked back to the original pickled and oil steel that it came from
So now we know all of our backing plates are stamped to the correct specifications
And since this container is full we could take it to the next step at the mechanical attachment
Facility and just so you get an idea the size of this facility
Let's go for a quick ride on the forklift
This company has a total of seven hundred thousand square feet of floor space and all those orange bins that you see that are stacked
Up. Those are all filled to the top with backing plates for almost every car produced in the world
And here we are making brake pads specifically for my truck. How crazy is that?
So now the forklift driver is bringing the backing plates to the next step which is adding the mechanical attachment to the backing plate
So we have the backing plates that we just stamped and these are going into the NRS machine. This machine is also oppressed
But it works a bit different than what we just saw
So the worker places a bunch of backing plates into the hopper which feeds the press to get you guys the best view they stop
The press for me and I literally went inside the press to set up cameras
So you could see what happens to the backing plate check this out
The blank backing plate is fed into the press and then the press pushes down to scrape the surface of the backing plate to create
hundreds of sharp rasps that at work
Here's an up-close. Look of what these rasps look like
These are an important technology that allows the brake pad material to stick to the backing plate without using glue
Now after the brake pads get that mechanical attachment scraped into them
They get transported via conveyor belt and get collected into another orange bin
so we go from this smooth backing plate to a backing plate with hundreds of rasps on the other side that are gonna hold that
brake pad material on so with that we are done with our third step and
now the forklift operator could take the bin filled with the backing plates and bring it to the loading dock because the next thing we
Need to do is galvanize these backing plates and to do that. We have to bring them to a separate but nearby Factory
So after a short trip
We're at the galvanizing factory where our backing plates are hung on these racks so they could be coated with zinc
This process is gonna put a sacrificial layer to prevent the backing plate from rusting. So, let's see how it's done
There are seven main steps for galvanizing backing plates first
The rack of backing plates is dipped into a heated water and sodium hydroxide bath
Which removes grease from the surface of the backing plates?
Next it comes out of that bath and gets dunked into plain water to rinse off the backing plates
Then it goes into a pickling bath where acids clean any surface
rust and scale off the backing plates then the rack gets submerged into water again to insure the acid is rinsed off and now the
Backing plates are placed in an aqueous solution and an electrical current is run through them
So the zinc ions attach to the backing plates
Now the zinc is bonded to the surface of the backing plate and a thin even layer to provide rust resistance
then the rack goes into a post treatment sealer which improves corrosion resistance and
finally the last step is to do one last rinse in plain water and
Pull it out to let it dry
After it dries all the backing plates are officially zinc coated and therefore rust resistant and ready for the next step
So let's head back to the brake pad Factory and back at the brake pad factory
Our freshly zinc coated backing plates are about to look like a brake pad
Because the next thing we're gonna do is add the brake pad material now
There are three main ways to add friction material to a backing plate and the first method which this factory doesn't do
But I wanted to cover is gluing the friction material
This is actually really common for brake pad manufacturers to do they get a bare piece of metal because you can't have galvanization
Because the glue won't stick to it. You also don't have that mechanical attachment
You have a nice flat bare piece of metal and they use heat and pressure to glue the friction material
Onto the pad now since it's not galvanized it can't be protected by rust
So what they do is they paint it so you get a painted pad like this now
This is what my truck was using and this is common on many aftermarket pads now
The second method is molding the friction material. This Factory does do that
And what they do is they get a mold they put the backing plate in there
They pour the friction material in and then they use heat and pressure to cure that friction material
Against the rasps against the backing plate so that mechanical attachment
Holds it in and then for the third method this is called the fusion process
It's the newest technology in the brake pad industry, and we're about to get a sneak peek
So let's go check it out
What you're looking at is the fusion machine and here's how it works
First the worker places the friction material into the holder followed by the backing plate with a mechanical attachment facing down into the friction material
next the fusion machine rotates and brings the backing plate and friction material to the press the press pushes down with
1200 psi of pressure to join the friction material and backing plate as one solid piece
There is no heat used here
Instead the sharp mechanical attachment on the backing plate is pushed into the friction material and then it's slightly bends poking into the friction
So it can't come off finally the machine spins again and a vacuum picks up the brake pads and places it on a conveyor belt
To be brought to a worker who will package the brake pads
this is a much cleaner and more efficient method than gluing the friction material or even molding the friction material and
There we go. Our friction material is on our backing plate
But there's one more step we need to do and that is make the brake pad shim which starts out as this rubber-coated
coil of steel which is
Straightened out and makes its way to the press the press then stamps out the brake pad shim and these shims are used to isolate
The brake head from the caliper to keep the vibrations and no down
so let me show you one of these up close all it is is a thin rubber coated piece of metal that goes on the
Backing plate. That's all you need to make the brakes a little bit quieter now while it's simple it's important
So let's get it on the back of our brake pad
And all you have to do is snap it on good now we've officially made our own brake pads from start to finish
so let's package them up getting all four brake pads in here as well as the stainless steel brake hardware and the piston cushions and
Now, let's fold the box up and close it, but we aren't done yet
the last step in the brake
Manufacturing process is done here at the research and development and testing facility where they have a brake dynamometer
They have a shear test machine. They have a saltwater corrosion chamber
So what we're gonna be doing is we're gonna be testing the brake pads that we made and as a little comparison
We have some painted brake pads just to see the difference. So let's go get these on the dyno
This is the brake pad. Dyno
So I'm gonna hand over the brake pads that we just made to the lab technician and he's gonna install them in the caliper then
The doors are closed for safety because we're about to torture test these brake pads
To make sure they could hold up to the harshest conditions
So with a hit of a button the dyno starts up and spins the brake rotor to highway speeds and then we're gonna do multiple
Panic stops like if there was an accident in front of you and you had to slam on your brakes to come to a complete
stop
The only difference is we're gonna do this over and over until the brake rotor is brought up to 600 degrees Celsius
Which makes it glow red? Hi, this is pushing the pads to the extreme limits
So extreme chances are you'll never see this on the road and we're gonna be doing this for both the galvanized end Tainted peg
Which will get ready for the next test the corrosion chamber test
So here's the painted brake pad and the galvanized brake pad after the dyno
The idea is to give them some wear and tear so we could test them in the corrosion chamber
This is the corrosion chamber which uses salty humid air to simulate about two months of winter driving
So the lab technician is gonna put both the galvanized pad and the painted pad in the corrosion chamber so we could see the difference
So with the lid closed the salty humid air is being circulated and we have to wait about a day for the tests to complete
And a day later, we are ready to see the results. So let's remove the pads from the corrosion chamber and check this out
Right away, you can see the painted pad has rust on it and the paint is peeling off the backing plate
And remember this is after a simulated two months on a winter road
And then with the galvanized pad the zinc does its job it provides a sacrificial layer and protects the steel and prevents it from rusting
So it's pretty cool to see how the galvanization prevents the steel from rusting. Now, let's take these two pads to the shear test machine
This right here is the shear test machine and let me show you what it does
So this black metal piece is gonna push on the side of the brake pad and measure the force it takes to break that friction
material off now
we're gonna load the brake pad into the holder add the top plate over the pad and
Lower the top arm to hold it in place. Now. The gauge is on the right are reading the force
it takes to break the brake pad material off and the top is the mechanically attached pad and the bottom is the glued pad so
Let's start the test right now. The force is increasing until the brake pad fails
And you can see the glue pad just failed and the mechanically attached pad is still going and there you go. Finally it failed
So it took more than double the force to break it
so with the painted pad the glued friction material popped right off and with the galvanized pad you can see the hooks held on to
The friction material and what's really cool? This is the brake pad that we made and while it's awesome to see lab results
Let's go out into the real world and test this out and instead of driving some fancy sports car
This is gonna be my test vehicle. It's a Chevy Tahoe
It weighs over 5,000 pounds a nice heavy vehicle something that regular people drive and it's really gonna put these brakes to the test
So let's go get these installed
so we're gonna install the galvanized brake pads in the of this SUV just like that and then we could install the brake caliper and
Finally tighten down both bolts. So they're snug and we're ready to go. Now. We're gonna torture test the brakes by doing repetitive hard stops
So I need to floor it and then head down the track wide open throttle
Until I hear a beat, which means I hit 60 miles an hour
Now I'm hard on the brakes until we come to a complete stop and I'll be doing this over and over and over and finally
after fifteen panic stops
the brake pads caught fire and the temperature of the brakes were just under 600 degrees Celsius or about
1,100 degrees Fahrenheit, so we really put these brakes to the test today and we got to experience that firsthand
So there we go. How cool is this?
We start out with a coil of pickled and oiled steel then we stamp that to make a backing plate
We added a mechanical attachment using the NRS
Press then. We galvanize it to prevent rust then we added our semi metallic friction material
We add a shim to prevent brake noise
And finally, we have our completed brake pad and that's everything on how brake pads are made from start to finish
So now there's one more thing we need to do and that is fly home
To good old New Jersey and install our brand new brake pads
so out with the old rusty brake pads that are stuck in here and look at how rusty these are then we could remove the
caliper to give us access to remove the old rotor as well now in with the new rotor torque down the caliper to spec and
Now we're ready to install the brake pads
So let's get the new stainless steel hardware
Installed into the caliper and these just snap into place and allow the brake pads to move freely along a smooth clean surface
Good now we'll add some anti-seize onto the brake caliper pistons and let's install the included
Piston cushions and these are something new to the market and they help prevent the brakes from making noise due to rubbing against the bare
Metal caliper Pistons, you just need to push them into the piston and that's all there is to it. All right
so with our piston cushions in and our brake hardware in there's one last thing we need to do and that
Is install the brake pads that we made I like to add a very thin coat
A nice ease to the back of the caliper and to the brake hardware and this helps prevent brake noise and keeps the pads moving
Freely, now we can add the pads and it goes right into place just like that and notice how easy these go in
that's why it's important brake pads are built to tight tolerances and Oh a speck then we could close up the caliper and
Finally, we could tighten down the caliper bolt and we are done. So
There we go out with the old
rusty seized up brake pads and in with the nice brand new ones and the best part is
We learned how they are made from start to finish
This was easily one of my most favorite videos to make ever
What an experience and how cool is it to actually see how brake pads are made?
It's one thing to install them in your car
It's another thing to learn what goes in to making brake pads now
I do want to thank NRS breaks for supporting the video and making this possible
you guys didn't see what went on behind the scenes but they shut down part of their factory so I could go and film and
Show you guys each step of making brake pads
Not only that we got to see things that not many people get to see I got to get it on camera and share it
With millions of people so we can learn how brake pads are made. And again, thank you very much
I'm gonna link their brake pads in the description so that if you guys need brake pads
You saw what goes into them you saw the quality, you could find them down in the description
I think it's pretty cool to run brake pads that you actually know how they're made speaking of how it's made
This is my first time making a video like this
Normally, I do how to replace brake pads or how to replace a wheel bearing not how it's made
let me know in the comments what you guys thought is this something that you want to see me continue doing we can make a
little series out of it
Hopefully other brands reach out and we could see how I don't know wheel bearings are made or tires are made
Comment some ideas down below if you like this and as always if you enjoyed the video remember to give it a thumbs up also
If you're not a subscriber consider hitting that subscribe button for more videos just like this and finally again
I'm gonna link this brand brake pads in the description go check them out
I'll also link a video on how to replace brake pads from start to finish that goes in-depth so
You know exactly how to do it yourself
Posting Komentar
Posting Komentar