How to Replace Radiator 06-09 Chevy Equinox
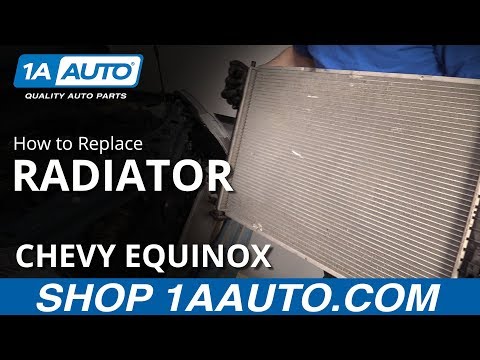
1A Auto Parts:
How to Replace Driveshaft U Joints 07-14 Chevy Suburban
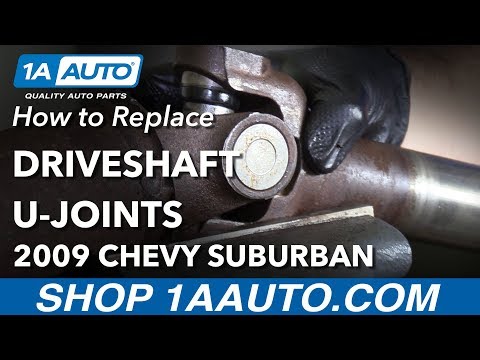
1A Auto Parts:
How to Replace Front Exterior Door Handle 14-17 Chevy Silverado

1A Auto Parts:
GM 3.0/3.6L Timing Replacement, Cloyes 9-0753S
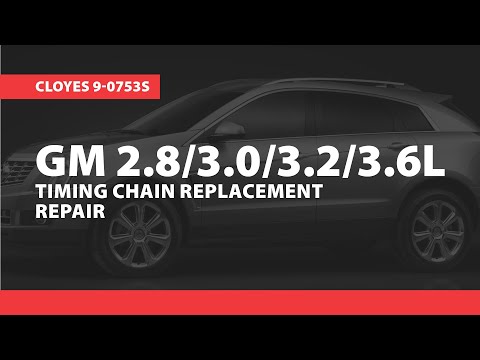
Cloyes Gear & Products, Inc.:
Hi, I’m Cody Smith, Technical Support Manager for Cloyes Gear and Products.
In this video I’m going to show you how
to service the timing chain components in
the GM High-feature V6 engines from 2007 to 2015 as of mid-2016.
We will be using Cloyes aftermarket replacement components.
Components we are going to be using today.
This is the 9-0753S kit.
It will contain the chains, tensioners, guides,
the idler sprockets, and the crank sprocket.
The timing component service of this engine
can be done with the engine in the vehicle.
To begin remove the intake manifold, the camshaft
covers, and the front engine cover to access the timing drives.
Once the chain drives are accessible, rotate
the engine to the stage two timing position.
Align the crankshaft sprocket timing dot to the dot on the oil pump at about the eight o'clock position.
A key point about this application the timing system is composed of three drives subsystems
and uses two stages for timing alignment.
Stage one aligns the left bank secondary and
primary drive systems,
and stage two aligns the right bank secondary drive system.
Note, once the chains are removed, take care
when rotating the shafts individually.
This is an interference engine.
We’ll begin with the removal of the right
bank secondary drive system.
Remove the right bank secondary camshaft drive
chain tensioner,
tensioner guide,
chain guide,
and then the chain.
Now that the right hand bank components are
removed, rotate the engine to the stage one timing position.
Align the timing mark on the crank sprocket
to the timing mark on the oil pump at about the five o'clock position.
Next we are ready to remove the primary drive system.
Remove the primary chain tensioner,
the upper
guide,
and then the primary timing chain.
Note that we are leaving the primary guide
in place.
Later we will discuss the reason for this.
Remove the right hand idler sprocket.
We are now ready to remove the left bank secondary
drive system.
Remove the left bank secondary chain tensioner,
the chain guide,
the tensioner guide,
then the chain.
the left hand idler sprocket.
Now remove and replace the crank sprocket.
Now is the time to remove and replace the
VVT cam phasers if necessary.
During the replacement of the phasers, use
a wrench on the camshafts hex features
to hold the shafts while removing & torqueing
the camshaft bolts.
Re-torque the new bolts to 43 foot pounds.
Before we start the installation I have a
few things to show you.
All 3 timing chains have colored timing links.
The two secondary will have two similarly
marked links that align to the camshafts,
and the one unique marked link that aligns
to each respective idler.
The primary chain has 3 uniformly marked links
that align to the two idlers and crankshaft.
The marked links on the primary chain are
evenly spaced so alignment is symmetric.
The tensioners are shipped in the deactivated
state with the activation pins installed.
They must be installed in this deactivated
state or damage will occur.
In the event of installing a tensioner that
has already been activated, you must go through the deactivation procedure.
To deactivate a tensioner that has been activated
remove the piston assembly from the tensioner housing,
and compress and turn clockwise on
the ratcheting cage mechanism until it stops.
Now reinsert the piston assembly into the
housing, compress, and insert the pin.
Note the tensioners are also shipped with
the gaskets that utilize a tab feature to index the tensioner bolt threads.
It is best to install the gaskets with the
tensioner bolts before installation on the engine.
The lower primary guide that we left on engine
during timing component removal
is attached using critically torqued oil pump attachment
bolts.
Unless you are servicing the oil pump it is
best to not remove the lower guide bolts,
because it will disturb the oil pump’s properly
torqued two-piece housing.
Cloyes recommends replacing the nylon shoe
using the nylon from the provided guide assembly in the kit.
Use a small tool to separate and remove the
nylon shoes from the steel guide brackets,
and reinstall the new nylon shoe on the engines
original bracket.
We will start the assembly with the left bank
secondary drive system.
Install left bank camshaft drive chain along
with the intermediate drive chain idler.
Align the similarly marked links of the chain
to the “L” timing marks of the VVT cam sprockets,
and the unique marked chain link
will align with the hole on the intermediate idler.
Torque the idler bolt to 43 foot pounds.
Install left bank tensioner guide.
Torque the bolts to 18 foot pounds.
Next install the chain guide.
Once again torque to bolts to 18 foot pounds.
Install left bank secondary tensioner and
install the attachment bolts to 18 foot pounds.
Re-check timing alignment,
and pull the pin
to activate.
Now we are ready to assemble the primary drive
system.
Install the right bank intermediate idler,
and torque the bolt to 43 foot pounds.
Install primary camshaft drive chain.
Align the marked links of the chain to the
timing marks of all three shaft sprockets.
Install primary upper chain guide, and torque
to 18 foot pounds.
Install the primary chain tensioner, and you
guessed it, torque the bolts to 18 foot pounds.
Verify the timing alignment once again, and
pull pin to activate.
Now with the left bank and primary systems
assemble, we are ready to install the right bank components.
You are going to want to first rotate the
engine back to the stage 2 timing position.
Align the timing mark on crank sprocket to
the timing mark on the oil pump at about the eight o’clock position.
Install the right bank secondary chain.
Align the similarly marked chain links to
the “R” timing marks of the VVT cam sprockets.
Align the uniquely marked link to the hole
in the right hand idler sprocket.
Now install the chain guide.
Torque the bolts to 18 foot pounds.
Install the tensioner guide.
Torque bolts to 18 foot pounds.
Install the right bank tensioner.
Once again, torque bolts to 18 foot pounds.
Re-check the timing alignment, and pull pin
to activate.
You are now ready to reinstall your timing
cover, camshaft covers, and intake plenum
using proper torque specs and tightening sequences.
If you have any questions please call our
tech line.
Please subscribe to our channel.
How to Replace Serpentine Belt 14-19 Chevy Silverado
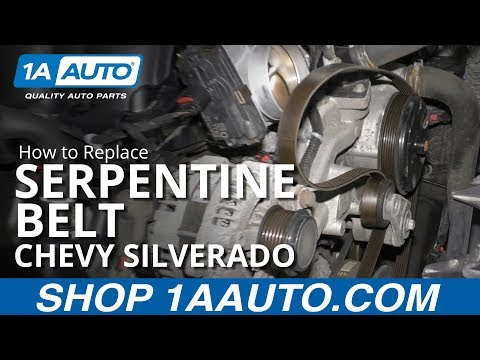
1A Auto Parts:
GM 2.0/2.2/2.4L, Timing Replacement, Cloyes 9-4201S & 9-4202S
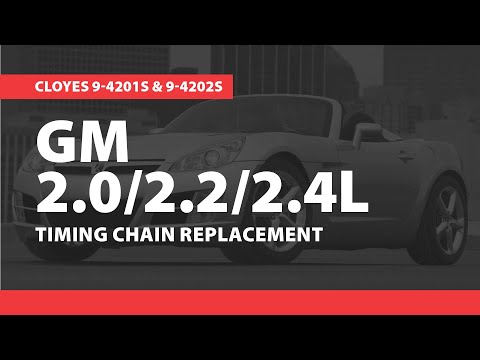
Cloyes Gear & Products, Inc.:
Hi I'm Cody Smith tech support manager
for Cloyes Gear and Products,
and this is version 2 of our Ecotec timing chain replacement video.
We received great feedback on our first video, but we wanted to expand on the original,
address some commonly asked questions,
and touch on later model VVT equipped engines.
Cloyes offers a full product line of
components and kits for the Ecotec engine.
Here's a look at the timing
components we will be installing in this video.
Primary timing chain set, part
number 9-4201S, comes with the chain,
tensioner,
guides,
sprockets,
the cam sprocket bolts, and the new
oiling nozzle.
And the 9-4202S balance shaft kit will include the
balance shaft chain,
tensioner,
guides,
and sprockets.
We also offer a primary timing
chain kit for variable valve timing applications that comes without cam
sprockets. Part number 9-4201SA.
And sprocketless kits for both primary and
balanced shaft systems 9-4201SX and 9-4202SX respectively.
Please visit the buyer's guide on our website for application lookup.
Timing system replacement can be done with the engine in the vehicle.
To get started remove the valve cover and the front engine cover to access the timing and balance shaft components.
With the covers off, but before removing any components,
rotate the engine and number 1 top dead center on the exhaust stroke.
This is the position the engine needs to be in for timing chain installation.
To do this there are only two things you need to look at...
the position of the crankshaft
key, and the timing marks on the cam sprockets.
When the crankshaft key is at
12 o'clock number one is at top dead center.
However you need to make sure you're on the correct stroke.
To verify the stroke make sure the intake mark on the intake cam sprocket is at about the 2 o'clock position,
and the exhaust mark on the exhaust cam sprocket is at about the 10 o'clock position.
If the cams are in these positions you're all ready for disassembly.
If the cam marks are opposite just rotate the crankshaft one full revolution and check again.
If the timing system is failed take care and rotating individual shafts due to
possible piston to valve contact.
This is an interference engine.
Let's start with the disassembly.
Using a 32 millimeter, or inch and 1/4 wrench or socket, remove the
primary tensioner.
Remove the upper guide.
Next remove the exhaust cam sprocket
using a 24 millimeter or fifteen sixteenths wrench on the camshafts hex feature to hold the camshaft.
Discard the cam sprockets torque to yield bolt.
Remove the tensioner guide through the cam drive chest.
Next using a 10 millimeter hex drive remove left hand guide bolt access plug then remove the left hand guide.
Remove the intake cam sprocket and
discard the torque-to-yeild cam sprocket bolt.
You can then remove the chain through
the top of the engine.
Remove the crank sprocket. Ensure the key
stays in place.
Now go ahead and remove the oil nozzle.
Now we can start with the
balance shaft components.
Start with the balance shaft tensioner.
Now remove the
balance shaft tensioner guide,
followed by the left-hand balance shaft chain guide,
and then the upper guide.
Now remove the balance shaft drive sprocket or inner cranked sprocket
followed by the balance shaft chain.
Using a 5/32 punch or drill bit in the hole on the balance shaft bearing carrier
engage a tooth of the balance shaft sprocket to hold the shaft and remove the bolt and sprocket.
Repeat this process on the other side.
Also note this is the water pump.
If you plan to replace the pump, now is the opportune time to do so.
Before we get
started on the installation here are some things you need to know.
Let's start with the chains.
GM has had several variations of markings on the primary and balance shaft chains over the years.
Here is Cloyes current design chain with one yellow marked link and two black marked links.
The same principle applies to all
the different designs.
There is one uniquely marked link which always aligns to the mark on the respective intake shaft sprocket,
and two similarly marked links that align to the marks on the exhaust sprocket and the crankshaft sprocket.
See our current chain and instructions on our website.
For those of you with a later model Ecotec engine equipped with variable valve timing...
You're gonna see a difference in the cam sprockets.
VVT equipped engines use a phaser assembly as opposed to standard cam sprockets.
Despite the difference in appearance and functionality there is little difference in installation.
The marks on the phaser assemblies still
align to the color timing marks of the
chain in the same locations,
and like the earlier sprockets, the phasers will only index under the camshafts one way.
The phaser attachment bolts are torqued to yield just like the non VVT sprocket bolts;
however, they do have a different torque specification.
Tighten VVT phaser attachment bolts to 22 foot-pounds
plus an additional 100 degrees.
GM does offer a cam phaser holding tool for the torquing process;
however, the process we show in this video without the tool is acceptable.
If your engine is turbocharged or supercharged pay
attention to this.
GM used a different inner cranked sprocket to drive the
balance shaft chain on forced induction engines.
The inner cranked sprocket
included in the 9-4202S, balance shaft chain kit,
will not work due to an overall thickness difference between the two designs.
The original sprocket must be reused or replacement must be sourced.
Cloyes does not offer this sprocket.
All Cloyes aftermarket balance shaft sprockets are an improved
design that eliminate the OE cushion rings.
The sprockets are a direct and
improved replacement to the originals.
The sprockets are marked intake and exhaust so ensure to install the sprockets on the correct shafts.
Both chain tensioners used in the Ecotec engines must be installed in their
deactivated state,
and activated against the tensioner guide.
The balance shaft chain tensioner uses a pin that is simply pulled after installation toactivate the tensioner.
Due to the ratcheting mechanism, the tensioner cannot be installed in the activated state.
To deactivate a balance shaft chain tensioner that has been installed and activated,
you must turn the piston 90 degrees,
compress the piston,
turn it back 90 degrees,
then insert the pin.
Do not use any gasket or silicone when installing this tensioner.
The Ecotec primary tensioner has been through three design changes.
The first was a two-piece design with an o-ring.
Second was also a two-piece design, but the o-ring was removed.
And third is a captive one-piece design.
Cloyes supplies the latest version that supersedes all previous designs.
The tensioner has an internal ratcheting mechanism that requires the tensioner to bedisassembled in the event that an activated tensioner needs to be deactivated.
A deactivated tensioner will allow the piston to be pulled in and out freely.
This is the state the tensioner must be installed.
An activated tensioner will have spring pressure behind the piston.
To deactivate an activated
tensioner you must remove the snap ring and pull the inner assembly out of the
housing .
Then compress and turn the cage assembly clockwise until it stops.
When released the assembly should stay compressed.
Now reinstall the assembly back into the housing and reinstall the snap ring.
The activation process for this tensioner will be discussed later.
We are now ready to start the
installation.
Start by installing the improved balance shaft sprockets.
Remember to install the correct sprocket on each side.
Utilize the same punch or
drill bit used during disassembly,
and torque the bolts to 37 foot-pounds.
Next install the inner crank sprocket.
Followed by the balance shaft chain.
Note the balance shaft system must be
properly timed to prevent excessive engine vibrations.
As I explained earlier start with the uniquely colored link of the chain and align it to the mark on the intake balance shaft sprocket.
The mark on the intake sprocket should point straight up to 12 o'clock and align with the colored link.
Next move over to the exhaust side and align the similarly colored link to the mark on the exhaust sprocket at about the six o'clock position.
Wrap the chain around the water pump and align the other similarly colored link to the mark on the crank sprocket at about the six o'clock position.
With the chain installed on all sprockets go back and make sure all marks are still aligned properly.
We can now install the balance shaft chain guides.
When installing the guides make
sure the chain is installed between the raised edges of the guides contact
surfaces.
Start with the upper guide.
Followed by the left hand guide.
Then the tensioner guide.
All balance shaft guide bolts torqued to 89 inch pounds.
Install the balance shaft chain tensioner, and torque the bolts to 89 inch pounds.
Ensure timing marks are all still aligned, and pulled the activation pin.
Before installing the oil nozzle make sure the passage is free from oil sludge
and debris.
Torque the bolt to 89 inch pounds.
Now install the crank sprocket.
We can now install the timing chain.
Wrap the chain around the intake cam sprocket with the uniquely colored chain link aligned with the intake cam sprocket timing mark.
Feed the chain down through the cam drive chest ensuring the chain goes around both sides of the engine
block casting bosses,
and work the bottom of the chain over the crankshaft nose.
Then install the intake cam sprocket and hand tighten the new torque to yield cam
sprocket bolt.
Make sure the sprockets indexing features index completely into
the camshaft.
Install the tensioner guide through the cam drive chest and torque
the bolt to 89 inch pounds.
Install the exhaust cam sprocket with
the exhaust timing mark on the similarly color chain-link align.
Loosely install the cam sprocket bolt leaving the sprocket key feature disengaged from the
camshaft.
Use a 24 millimeter wrench to turn the intake camshaft counterclockwise to allow the exhaust cam sprocket indexing feature to properly engage with the camshaft.
While doing this you must also make sure that the crankshaft sprocket mark aligns properly with the appropriate chain link
timing mark.
If the crankshaft timing mark does not
align properly;
you can slightly rotate the crankshaft by hand in the appropriate direction and try again.
Once the exhaust cam sprocket is engaged, and all marks are aligned,
hand tighten the torque to yield bolt.
Install left-hand guide and torque the
bolts to 89 inch pounds.
Next install the left hand guide upper
bolt access plug using some thread
sealant on the threads.
The plug torques to 66 foot-pounds.
Install the primary chain tensioner.
The tensioner torquesto 55 foot-pounds.
Before activating the tensioner, shift all chain slack to the tensioner side using the harmonic balancer,
and note the amount of slack gathered above the crank sprocket.
Verify once more that all timing marks are
still aligned properly.
Now using a soft tip pry bar, or similar
tool,
reach down through the cam drive chest and apply pressure to the chain at
the top of the pivoting tensioner guide.
For the tensioner to activate you must
compress the tensioner approximately 1/8 of an inch then release.
Once released the internal spring of the tensioner will be operational and you should notice most of the chain slack taken out.
With the tensioner activated you
are now ready to torque the torque to yield cam sprocket bolts.
Use a 24 millimeter wrench on the camshafts hex features as backup during the process,
and tighten the sprocket bolts to 63 foot pounds plus an additional 30
degrees.
Now install the upper guide. Torque the
bolts to 89 inch pounds.
The engine is now in time. It is not
advised to rotate the engine by hand beyond this point.
If the engine happens to be rotated,
the colored timing marks on the chain will not immediately come back around and realign to the marks on the sprockets,
but the sprocket timing marks will come back to their original positions every
two rotations of the crank.
You can now install the front cover and the valve cover.
The front cover bolts torque to 18 foot pounds, and the valve cover bolts torque to 89 inch pounds.
Thanks for watching.
If you have any questions
please call our tech line,
and please subscribe to our Channel!
How to Change Tie Rods (inner and outer tie rod ends)
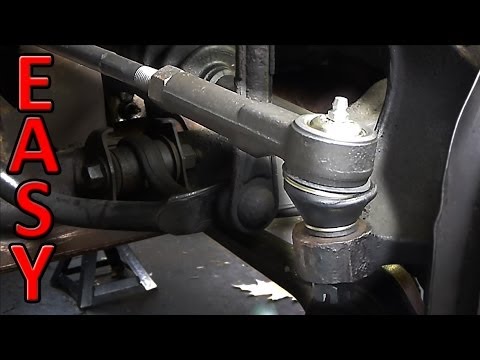
ChrisFix:
Hey guys Chris fix here and today I am going to show you how to replace the tie-rod ends
both the outside and the inside tie rod
ends
very important for your steering and for
your toe
alignment so I am going to show you how to do that now, so there is your tie rod
you can see I can move this with my hand, it is very old
300,000 miles will do that to it. It is amazing they made it that far
so here are all of the tools you are going to use for this job. You need
a couple wrenches, screwdrivers, flathead
screwdrivers
some lock tight thread glue
a torque wrench, a breaker bar, hammer,
rubber mallet, needle nose plyers
and a grease gun and the new tie rod
inside and outside. You will also need an inner tie-rod tool
which is this right here. You can rent
this for free Autozone or Pepboys or
whatever the main part stores you use.
So what you are going to do is take your needle nose plyers
and open up the cotter pin so that it is straight.
And once the cotter pin is straight, grab the other side
and start pulling it out.
there we go
one cotter pin pulled out.
Now you can put a 19mm or 3/4 ratchet or wrench on this.
A nice long break a bar will help.
Once you break it loose, use your ratchet
and take the castle nut off.
now there's a tool that you can use that
goes in here and pry's this up, but
what I am going to do is take this castle nut and I'm gonna flip it over
so screw it in this way.
Good! Now I am going to take a hammer, I'll use a rubber mallet just to be safe
and I will pop it up maybe up
[Metallic Hammering Noise]
There we go.
The tie rod end is out. Now this is the
interesting part
there's a nut here that they use for
your alignment
because this affects your alignment.
What you want to do is put your tie rod in and now we can unscrew this nut.
You just want to break that loose like that and now we can take this out and
you can see this spins freely... From the bottom here
that's that the bottom which is pointing down,
you wanna take this
and you want to spin it.
So that is one, two... and you want to count how many spins it takes to get this off.
three, four, five, six...
18, 19... So twenty spins total,
it took me 20 spins you get this off and
when you put the new one on
you want to count twenty spins and the
reason why is it that your alignemnt
isn't completely out of alignment. You are still gonna have to get the car aligned
after you change this
but at least your alignment wont be so bad
that it's dangerous to drive
so you could see this moves around very
easily and has a little bit of play inside and outside
so the inner tie rod end also needs to be changed, but we were going to do that anyway
Now you can see, so the tie rod end works by steering the car when you turn the steering wheel
it turns this which allows the car's
wheel to turn
it goes all the way up into here, and now there is a boot here
and you want to use a pliers to get
this off and there's also
a another one these except you have to break the clamp with a screwdriver,
and I will show you that now.
but that is all the way in the back
so for this one, you just get the
the same needle nose as before
squeeze it and pull it out.
all this is, is a little clamp to keep the boot on.
Now little trick here is to use a
screwdriver a flat head
and just bend this up a little bit. Not
too much because we are re-using the boots
you just want to get it under here so we can spray some silicone or grease
to make it slide off easier
Now we just go in here, with a flathead screwdriver,
carefully, without breaking the boot it's
like that
just like that... You see how the boot is up... get your WD40 or whatever
some type of grease or silicone, which is what I am using
and just spray it in there.
and that will make the boot come off a lot easier because surprisingly, the boot is on there tight.
the next thing we are going to do
you see that clip right down there
there is a clip right there, and what you are going to do is push the screwdriver in and turn the screw driver to open the clip
it's hard to see but I think you will get the idea when I do it.
You just get the screwdriver in there
and turn... [clicks open] and you can see
it opened up, and now we can take the boot off.
[Spray]
OK, unscrew this nut here so we can take the boot off.
take the bolt off, slide off your clamp,
now take your bellows boot off
good, so we're gonna wanna quickly
inspect this to make sure there are no cracks
looks good, so when we're installing
it there is this right here
that's gonna slide over the tube
in there
its going to slide over that tube which connects to the other tie rod on the other side of the car
it allows for venting... so you can see the
tube on the top right and then you could
see the
inside tie rod right there with its ball
joint that is
very loose, so now we're going to take
that out.
so here is the actual tie rod
the inside tie rod
and I just want to show you what is going to happen so that you completely understand this.
so here is your adapter
your adapter is going to fit on here, just like that.
So when you turn the tie rod too, it grabs the end and turns it
otherwise it would be hard to get a wrench
on here. You can do it you just have to see if you have
access. The other thing to remember is
that there's sometimes a pin in this
so you have to take that pin out and that is what I am going to go check for now.
You can see on this tie rod end there is a pin right here and this has to come off
so you take a flat-head screwdriver
you get underneith it, and you pry it out.
you could see I'm just prying this up
If you can't get your screwdriver under here that easy, you could use a hammer and the screwdriver
and just get it to indent a little bit. So you could see
I'm almost ready to just knock this thing out
Knocked it right out. So now we can unscrew this.
Just like I showed you, your adapter piece goes right on top just like that.
take your tie rod tool
slide it in
and then you put your ratchet on there.
Once you break it loose like that
this thing should come right out, and if it is not coming out easily
remember there's that pin in there that needs to come out first
here are the two tie rods side by side
the next thing you are going to do is make sure they are the same size
the new one is a little bit longer
so that is going to affect the toe but
we're getting an alignment anyway so
doesn't matter. Now you can see
I can move this really easily, that is the old one
a single finger can move it around
the new one... I cant even move it
it'll have to be on the car for me to move it. I'm going to get some blue thread lock
this is the removable type
and I am going to put a little inside here
Just like so... Now lets install the new tie rod.
never took the old clamp out
the clamp you have to break, take that out.
here is the pin
it's not really reusable
take our new tie rod
and just tighten it by hand
Once you cannot tighten it by hand anymore,
Once you cannot tighten it by hand anymore,
get your tie rod tool
put it over the tie rod
slide it on
then get your torque wrench,
for my vehicle it says torque to 66 to 74ft-lbs of torque
I am going to torque it to 70ft-lbs
Once you torque it, you are set.
I am under the car and you can see the hole for the pin.
That is where you push the pin in... I put a screwdriver head against the pin
like this... and then I used a hammer to lightly tap it in.
and now it's all the way in.
So remember before I was talking about the clip
that is a sacrificial clip that holds on
the boot that you put your screwdriver in here
and you twist and the clip opens up, well, it is only a one use clip
so either you get a new one, which
they're hard to find,
but one temporary solution is to use
zip-ties
I went to go get a bellows boot kit
to see if it comes with new clips and
and it came with zip ties
so although it sounds kinda cheap, the boot doesn't really move
very much so it's okay to use a zip-tie...
It is not a permanent solution like this metal clip
because a zip tie will eventually get
brittle but until you can find a metal clip
zip ties are a good way to go, and that is what I will use.
You can also use stainless steel hose clamps with the nut that tightens it down
The hose clamps are hard to find that are narrow enough to fit the boot.
so zip ties work nicely in this situation.
Now we are going to put the new boot on.
You see that at the end of my screwdriver?
There is that tube and you want to make sure you push
this into that tube... So I actually tightened up the zip ties
first up on the the boot, now I am going to slide the boot in.
so now you just tighten the zip ties after you push the boot all the way on
good
Now we take our clamp, and bring it up
Put it on just like that and we are done with the boot.
so here is the new tie rod end
we can see the new is nice and sturdy
the old one moves really easily. It comes
with all the accessories
the screw in the top, a pin, and a nut. So
they give you a new nut
but it's kinda small, so I will use the old one because it's thicker.
has more thread on it so it will lock
better.
Just screw that old nut back on...
It took me 20 spins to get this
off so I will put it back on with 20 spins.
It is threaded so we will start counting
1, 2, 3, 4, 5, 6 ,7, 8, 9, 10, 11, 12, 13...
14, 15,
16, 17, 18,
19, 20... OK
20 spins, face it down. Now will tighten
our nut up here.
We want the nut to push against
the new tie rod end.
This will keep it from moving.
I am going to put the grease valve on. Just screw it in by hand first.
Now I will use a 5/16 inch wrench
And just snug it down.
You dont want to tighten this too much.
Just enough, and that is good.
Now we will put this into the knuckle.
Line it up...
push it through...
Get your new castle nut and screw it on.
That is how it should look.
I set the torque to 46ft-lbs
And tighten it until it clicks...
[Click]
when it clicks once, you do it again and
in that statement
[Click]
And then that is tight enough.
we will now take our cotter pin and send it though the hole.
good
Now just bend the cotter pin around the castle nut
Like so
Now we're gonna lube this up
Put the grease gun on there and pump it with grease.
you can see the rubber expanding
and once it expands like that, that means you have enough grease in there
and you just finish the job!
You just changed the inner and outter tie rod ends!
Now go get your car aligned.
If the video was helpful, give it a "thumbs up"
and if you like how to videos, and this was good, then subscribe.
I upload how to videos weekly and it will help you save some money
and fix your own car.
If you want to see other "how to" videos, I will have links in the description.
You can also click on any of the videos on the screen.
How To: Replace Your Power Brake Booster

O'Reilly Auto Parts:
Hey everybody…
Chris here from O’Reilly Auto Parts to show
you how to replace a power brake booster.
If you’re noticing that it takes extra pressure
on your brake pedal to slow down, you might
be dealing with a failing booster.
Today I’ll be working on this 2008 Dodge
Nitro, but the basic procedure will be similar
on most vehicles with power brakes.
As always, know the specifics of your vehicle
before getting started.
And if you’re not completely comfortable
doing this yourself, we’d be happy to recommend
a professional technician in your area.
Any time you do work on your brake system,
pay attention to how your brakes function
before and after the job to make sure the
problem has been corrected.
Also, be very careful handling brake fluid.
It is highly corrosive and will damage any
painted surface.
Once you’ve got your supplies together,
here’s what you’ll do:
Chock your wheels and set the parking brake.
Pop the hood and disconnect the negative battery
terminal.
Set it aside someplace where it isn’t touching
metal.
You’ll need to relieve the vacuum pressure
that exists in the system so you can disconnect
the vacuum line and separate the master cylinder
from the booster.
To do this, pump your brake pedal a few times
with the engine off.
Once the pedal firms up, you’re good to
go.
Locate your power brake booster, which should
be right against the back wall of your engine
compartment on the driver’s side.
Before removing the booster, you’ll have
to remove the master cylinder, which is directly
in front of it.
In some vehicles, you can just move the master
cylinder to the side.
If you are able to move the master cylinder
to the side, there’s no need to unhook the
brake hydraulic lines.
And if you don’t need to remove the hydraulic
brake lines, the job won’t take as long
because you won’t have to bleed the brake
system.
If you do need to remove the brake lines,
leave the master cylinder cap on and remove
the master cylinder from the booster.
There’s no need to remove the fluid.
Hold your fingers over the holes as you remove
it from the vehicle to make sure no brake
fluid drips on anything.
Next, remove the electrical cable leading
to the brake fluid reservoir.
This can be done by hand.
Remove the clip that secures the connector
and push the tab to release it.
Unscrew the mounting nuts with your ratchet and socket.
Use the proper brake line flare wrench to
disconnect the brake fluid lines.
Put some shop towels in place and hold your fingers over the brake line as you remove
the master cylinder from the vehicle to make sure no brake fluid drips on anything.
Once you’ve removed the master cylinder,
tip it over your drain pan to allow any remaining
fluid to drain.
Keep in mind that brake fluid spills will
damage painted surfaces, so if this happens,
flush it with water immediately.
If your vehicle has antilock brakes, you’ll
also want to disconnect the brake line from
the hydraulic control unit, or HCU, and remove
this component so it’s out of the way.
Inspect the seal at the end of the master
cylinder… there should be no signs of brake
fluid seepage.
If you see fluid, there is a leak.
If this is not corrected, the new booster
will be damaged by allowing brake fluid inside
the vacuum chamber and deteriorating the vacuum
diaphragm.
So, if the master cylinder seal does show
signs of seepage, the master cylinder needs
to be replaced.
With the master cylinder out of the way, you
can turn your attention to the brake booster.
Inside the vehicle, tilt your steering wheel
up and remove the knee blocker to give you
easier access.
Your brake pedal attaches to a push rod that
leads directly to the booster.
Detach the retaining clip that connects the
two components.
Next, use your socket to loosen the four nuts
attaching the booster to the engine compartment
wall.
Back in the engine compartment, disconnect
the vacuum hose leading to the booster…
then slide the four studs out.
Tilt the booster up and carefully remove it.
Now, you’re ready to do everything in reverse.
Start by reading the documentation that came
with the booster to be aware of all warnings.
Then slide your new booster into position…
and use the four studs to secure it to the
wall.
Back under your dashboard, tighten the nuts…
and reattach the brake pedal to the push rod.
Lubricate the pin with the lubricant recommended
by the manufacturer… and ensure the retainer
safety clip is secure.
Replace the knee blocker panel.
Clean the mounting surface on the booster
thoroughly with a shop towel and brake cleaner
before attaching the cylinder.
Again, be sure not to get brake cleaner on
any painted surfaces.
Once everything is clean, use the nuts to
reattach the master cylinder to the booster.
Reconnect the vacuum hose…
HCU… and brake lines.
Reinstall the electrical wire leading to the
fluid reservoir.
Reconnect your negative battery terminal.
If you had to disconnect your brake lines,
you’ll need to bleed the brake system.
Now that everything is back together, start
your engine… and make sure your brake pedal
pressure has been corrected by testing your
brakes in the driveway before driving on the
road.
And that’s it.
You’ll find everything you need for this
and other jobs at your local O’Reilly Auto
Parts store or OReillyAuto.com.
Our DIY videos are designed to help answer
questions we get in our stores every day.
If you found this one helpful, subscribe to
our channel to get all the latest.
We’ll see you again soon.
How To: Replace Your Vehicle's Rearview Mirror
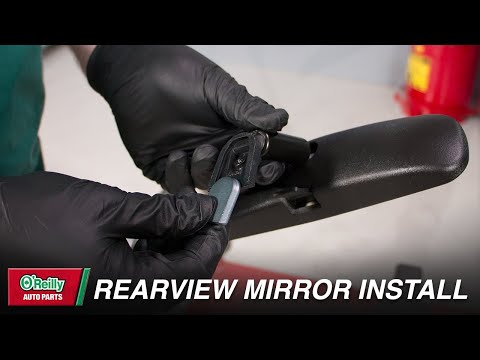
O'Reilly Auto Parts:
[Mechanical SFX]
Hey everybody. Chris here from O'Reilly
Auto Parts to show you how to reattach
or replace your rear-view mirror. Whether
you're putting the old one back up or
replacing it with the new one, these
directions should help. If you're not
completely comfortable doing this job
yourself we'd be happy to recommend a
professional in your area. Different
brands of adhesive may vary slightly so
be sure to follow the directions for
your brand that you have. As a general
rule only make the repair in
temperatures between 50 and 75 degrees
Fahrenheit. For our purposes, we'll be
demonstrating this on a small piece of
glass but the application will be the
same on your windshield. Start by marking
the outside of the windshield with a
crayon to indicate exactly where the
button was attached. Detach the mounting button from the mirror bracket.
Scrape the inside windshield glass and the mounting button thoroughly with the new
razor blade in order to remove all the
old adhesive. Always scrape in a
direction away from you. Glass can be
easily scratched so keep the razor as
close to parallel with the glass as
possible. If the mirror is mounted in the
dark strip at the top of the windshield
be especially careful. It's a good idea
to dust the dashboard at this point if
dust from the dash has stirred up while
you work. It could stick to the area of
glass you're about to clean. You also
want to use automotive glass cleaner to
remove all the residue of the old
adhesive from the inside of the
windshield. Open the cleaner activator
towelette and clean the marked area on the inside of the windshield. Allow two
minutes or wait until the area is
completely dry. Do not touch the
windshield. After priming, look at the
mounting button and be absolutely
certain about how it should be situated.
When you attach it to the windshield the
rounded end will be at the top and the
flat narrow side will be against the
glass. You'll only have one chance to
attach it the right way.
Open the adhesive and apply just one
drop to the center of the button. Too
much adhesive can run and cause problems. Immediately apply the button to the
windshield making sure the correct side
is up and hold it firmly in place for 60
seconds.
Most product will recommend waiting 15
to 30 minutes for the adhesive to set
but some professionals recommend 24
hours just to be certain the adhesive is
completely dry before mounting the
mirror to the button. Use this time to
clean the crown off the outside of the
windshield and once you've waited long
enough
reattach the mirror bracket to the
button. If the button is mounted
incorrectly, it's safer and easier
to bond another button on to the
original one rather than trying to
remove it and risking damage to the
glass. And that's it. You'll find
everything that you need for this and
other jobs at your local O'Reilly Auto Parts store or OReillyAuto.com.
Our DIY videos are designed to help answer questions that we get in our stores every day.
If you found this one helpful, subscribe to our channel to get all the latest.
We'll see you again soon.
How to Replace a Mass Air Flow Sensor on Your Car
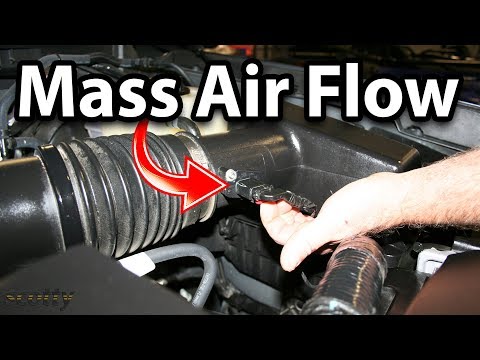
Scotty Kilmer:
one, two, three, four!
Rev up your engines!
It's time for the Scotty Kilmer Channel,
if your car is running poorly and sometimes
black smoke comes out of the exhaust,
then you could have a bad airflow sensor
on your engine, so today I'm going to
show you how to fix air flow sensor
problems in your car, now if you're lucky
you'll also have the check engine light
on so you can scan it for codes, just get
a scanner and connect it under the dash, then
read the code, in this case it's P0102
which is a mass airflow sensor problem
now we got lucky here because there was
a code for the mass airflow sensor, a lot
of times they won't trip codes, but in
this case it did, now in this Toyota
Camry it's real easy to find the mass
airflow sensor, you go to the air filter
box and there's a sensor right behind it
and it's really easy to take out, you
just squeeze the connector and pull that
off, then get a Phillips screwdriver
and unscrew it and pull it out and
here's the sensor itself, now sometimes
you can clean the sensors, you get some
mass airflow sensor spray and you spray
all the holes to clean any crud out, now
if you want to clean the sensor let it
dry about half an hour then put it back
in the hole, then after you put it back
in, reset the computer, just select erase
codes and yes and the codes will be
erased, then just drive the car around
and if the check engine light doesn't
come back on and it runs fine, you fixed
it by just cleaning it, but in these
Toyota's the sensors often go bad and
you have to replace it, so take a trip to
the auto parts store, then come back with
a brand new one and install it, just
place it in it's hole,
and put the two screws back on and then
snap the electrical connection back on
and as long as you're here, might as well
put a new air filter in too, they filter the
air going into the airflow meter, so you
don't want them dirty, a nice clean
filter can make the sensors last longer
and here's a mechanic's tip, don't buy
really cheap air filters, because if the
fibers get sucked into the engine
they'll go on to the airflow meter and
when air flow meter gets hot, they can
melt and ruin it, so buy quality filters
don't just go buy the cheapest ones you
can get your hands on, so the next time
your mass airflow sensor goes bad, now
you know how to fix it and remember if
you've got any car questions just visit
scotty Kilmer.com and i'll answer them
as soon as i get back from this ride!
Posting Komentar
Posting Komentar